Categorie: Industriebouw
Nieuwbouw wielstellenfabriek, draaistellenloods en een opslaghal NS
Haarlem
Gepubliceerd op 1 juli 2025
Tussen de monumentale werkplaatsen van NS Treinmodernisering in Haarlem, waar ooit de eerste treinen van Nederland vertrokken richting Amsterdam, wordt volop gewerkt aan de toekomst. Hier verrijzen onder regie van BBA en in uitvoering door K_Dekker een nieuwe wielstellenfabriek, draaistellenloods en een opslaghal van maar liefst 6.000 vierkante meter. Middenin de bedrijvigheid van het operationele spoorbedrijf, en te midden van nog vele andere projecten, voltrekt zich een indrukwekkend staaltje bouwkunst.
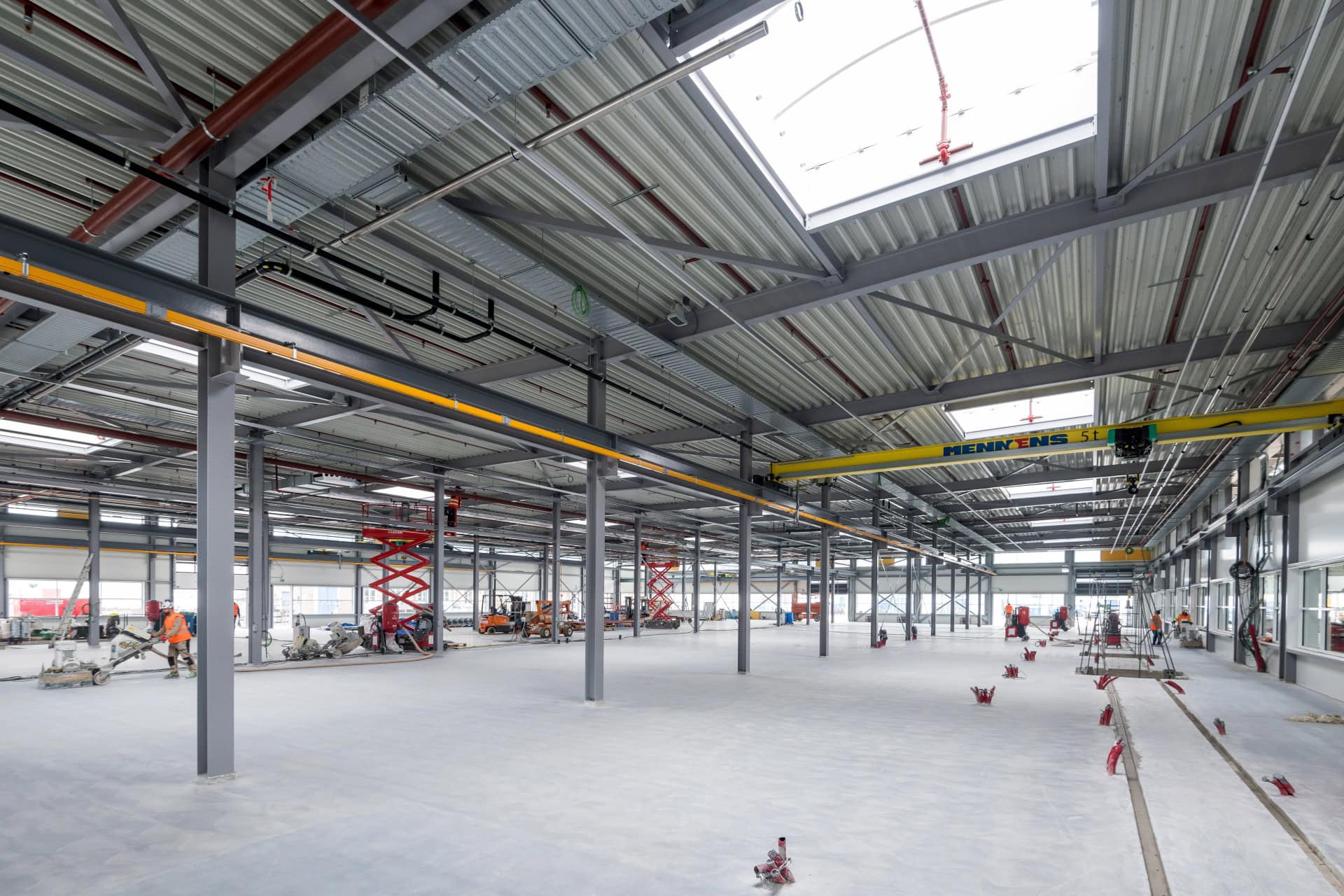
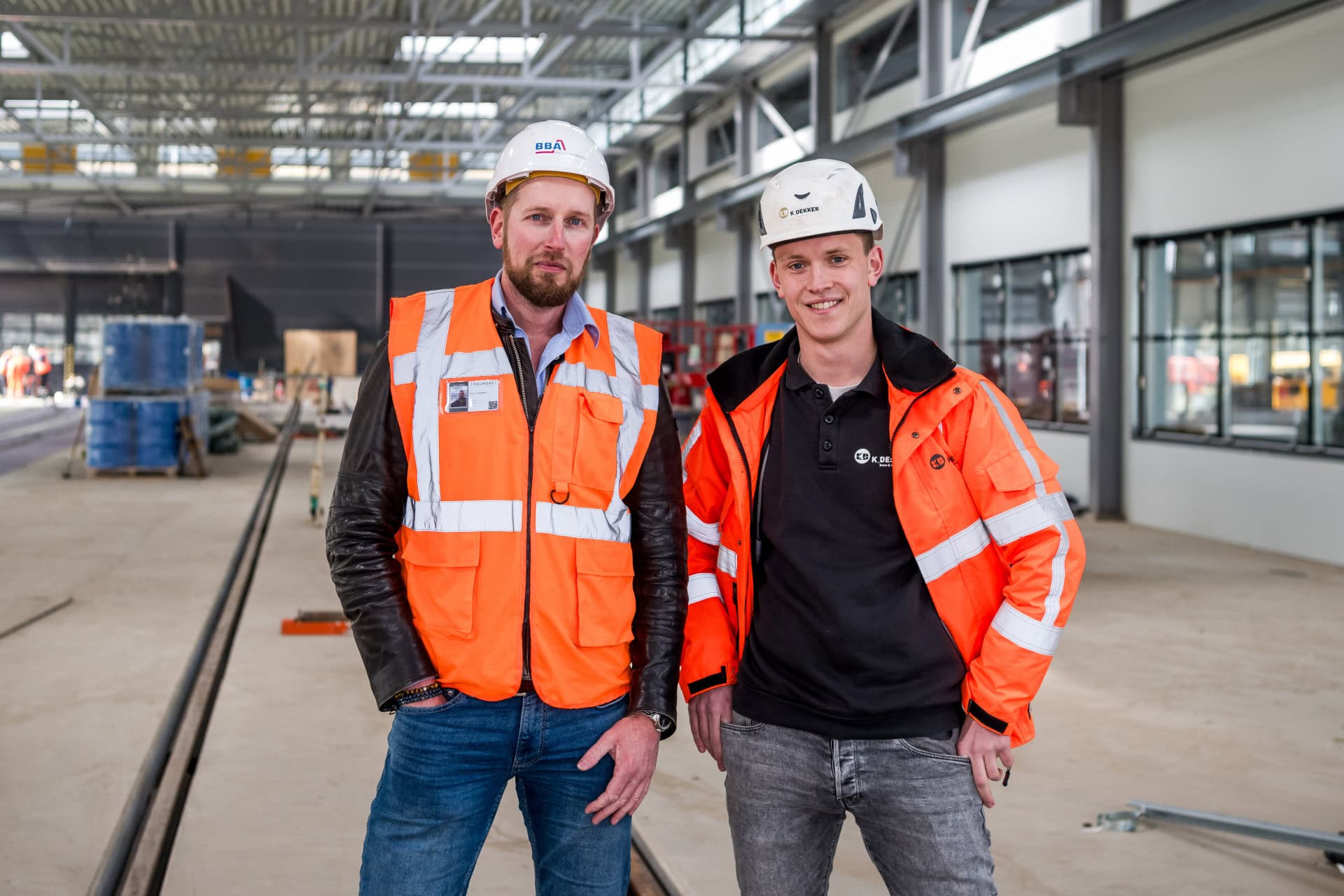
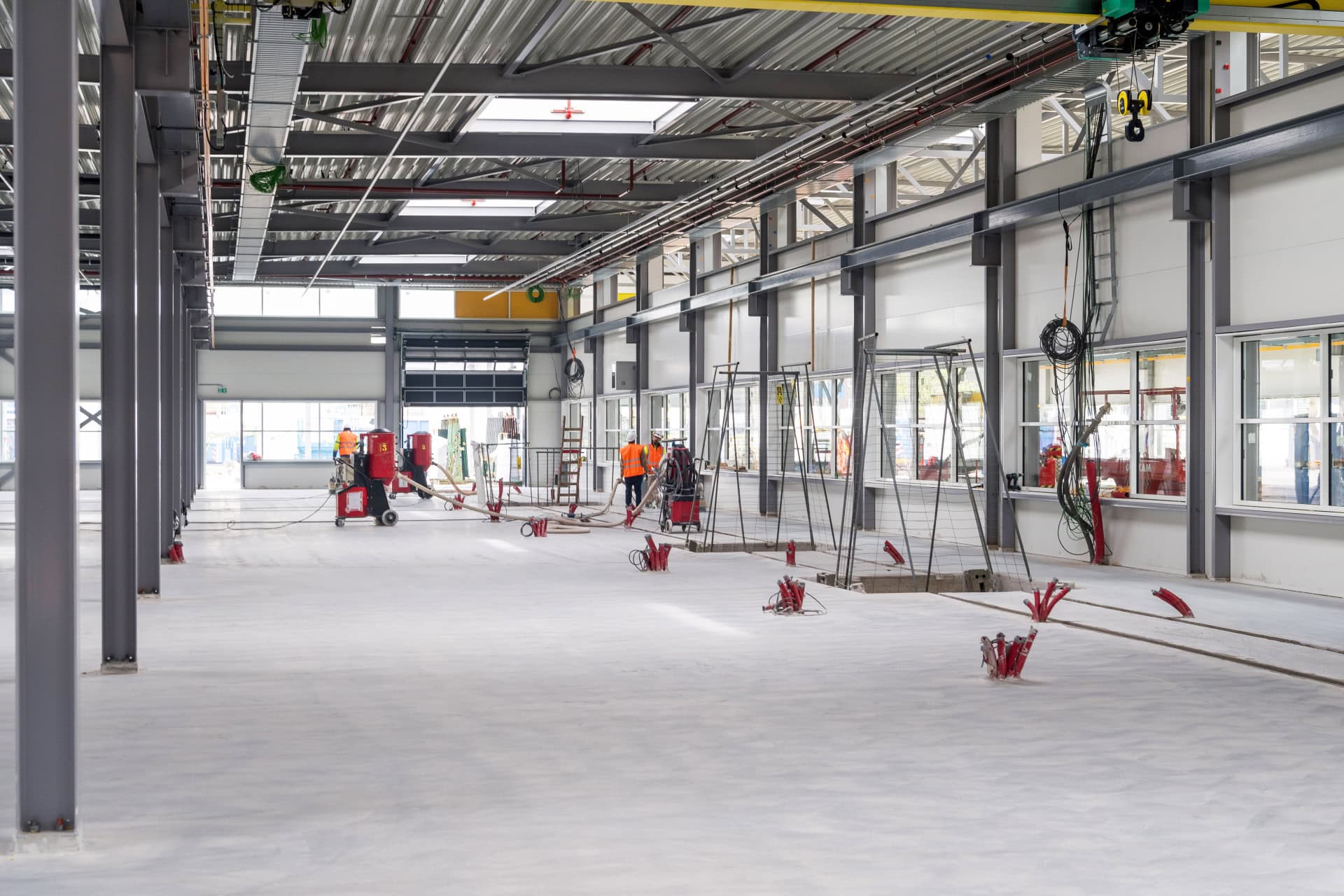
“Het is echt een bijzondere plek,” zegt Jesper Sterkenburg, uitvoerder namens K_Dekker. “Je werkt letterlijk tussen de historie, maar ook tussen de continuïteit van de Nederlandse spoorwegen. De fabriek moet doordraaien, want stilstand betekent hier niet alleen inkomstenverlies, maar uiteindelijk ook uitval van treinen.”
Rick Siebers, die namens BBA als gedelegeerd opdrachtgever de bouwdirectie voert, beaamt dat: “De productie mag geen moment stilvallen. Het vereist een enorme mate van afstemming en flexibiliteit, zeker omdat hier niet één project speelt, maar tientallen deelprojecten door verschillende aannemers.”
Drukke bouwplaats
De bouwplaats is een georganiseerde chaos. Heftrucks, vrachtwagens, hoogwerkers en bouwkranen delen de ruimte met treinstellen die dag en nacht in onderhoud zijn. “De bouwplaats is ongeveer net zo groot als het gebouw zelf,” vertelt Jesper. “Materieel past soms nauwelijks binnen het hek. Dan staat een hoogwerker buiten de bouwgrens en moeten we streng zijn. Maar de veiligheid staat altijd voorop.”
De samenwerking tussen de verschillende partijen op het terrein is volgens beiden essentieel. “We hebben een gezamenlijke transportplanning en een coördinator bij de poort,” legt Jesper uit. “Jamal wordt ingehuurd door K_Dekker en bedient voor K_Dekker de poort voor alle transporten. De transportplanning heeft K_Dekker ook zelf opgezet. Ze stellen Jamal beschikbaar voor transporten van de NS en andere aannemers op het terrein. Naast het transport voert Jamal controle op de bouwplaats van K_Dekker op het gebied van VGM (veiligheid gezondheid en milieu).”
Historische grond
De bouw vindt plaats op historische bodem. “Voordat we konden starten, zijn uitgebreide onderzoeken gedaan naar niet-gesprongen explosieven en archeologische vondsten,” zegt Rick. “Gelukkig is er niets gevaarlijks gevonden, maar het onderstreept wel de bijzondere locatie waar we werken.”
Die historie levert soms ook spanningen op. De stad Haarlem is als het ware om het NS-terrein heen gegroeid, wat leidt tot een ingewikkelde verhouding met de omgeving. “We hebben regelmatig contact met buurtbewoners,” aldus Rick. “Een bouwproject van deze omvang midden in de stad levert altijd klachten op. Maar tegelijkertijd zorgt NS hier voor heel veel werkgelegenheid.”
Technische uitdagingen
De complexiteit zit niet alleen in de locatie, maar ook in de techniek. “De nieuwe hal krijgt onder meer bovenloopkranen, zware funderingen en een innovatieve installatie om draaistellen te reinigen met droogijs,” vertelt Jesper enthousiast. “Daarnaast worden ook alle leidingen, goten en putten in eigen beheer gerealiseerd, iets wat normaal gesproken vaak prefab wordt aangeleverd.”
Prefab bouwen bleek hier nauwelijks mogelijk. “Alles wordt ter plekke opgetrokken,” zegt Jesper. “De staalconstructie, sandwichpanelen, betonvloeren – we doen het allemaal hier zelf, in weer en wind.” Hij benadrukt dat vooral de logistieke puzzel uitdagend is: “Je moet bedenken dat we werken in een gebied waar elke vierkante meter telt, met een continue stroom van treinen, onderhoudsploegen en goederenverkeer om ons heen. Soms moesten we onze kraan ’s nachts verplaatsen om de dagelijkse bedrijfsvoering van NS niet te hinderen.”
Ook het weer speelde een rol. “De hoge grondwaterstand en overvloedige regenval maakten het betonstorten en funderen extra complex. Iedere stap moest zorgvuldig worden afgestemd, zodat we geen vertraging opliepen,” vertelt hij. “Dat vergt niet alleen vakmanschap, maar ook een ijzersterke samenwerking tussen alle betrokken partijen.”
Samenwerking als sleutel
Zowel Jesper als Rick roemen de samenwerking. “We zijn allebei praktisch ingesteld,” zegt Jesper. “Geen ellenlange mails, maar korte lijnen. We stappen gewoon even bij elkaar binnen als er iets is. Dat werkt niet alleen sneller, maar voorkomt ook veel misverstanden. Soms botsen we wel eens even, maar het gaat nooit over personen. Altijd over het werk en over hoe we samen tot de beste oplossing kunnen komen.”
Rick vult aan: “Je moet eerlijk en direct kunnen zijn, zeker op zo’n complex project met zoveel partijen en belangen. Alleen dan kom je verder. Vertrouwen is daarin essentieel. Als er iets speelt, leggen we het direct op tafel. Zo blijft de samenwerking transparant en doelgericht.” Hij vervolgt: “Juist door die openheid en het wederzijdse respect houden we de vaart erin. En ondanks de druk en de hectiek kunnen we gelukkig ook samen lachen, dat maakt het werk een stuk prettiger.”
Vooruitkijken
De komende maanden worden spannend. De aansluiting van de nieuwe hal op de bestaande infrastructuur moet vlekkeloos verlopen. Dat betekent dat elk detail moet kloppen: van de exacte positionering van installaties tot de correcte afstemming van transport- en veiligheidsroutes. Ook start binnenkort de installatie van geavanceerde fabrieksmachines, waarvoor internationale partijen betrokken zijn uit onder meer Duitsland en Slowakije. “Dat wordt nog een uitdaging,” zegt Rick. “Zeker omdat sommige machines uniek zijn en voor het eerst in Nederland worden toegepast. Maar we zijn goed voorbereid en werken nauw samen met alle betrokken leveranciers en specialisten.”
Ondertussen kijken beide heren ook verder vooruit en maken zij al plannen voor de toekomst. “Na deze hal volgen nog meer projecten op het terrein,” vertelt hij. “Een parkeergarage, een kantoorgebouw, verduurzaming van bestaande panden… En daarnaast moeten er ook bestaande hallen deels worden gesloopt en opnieuw opgebouwd.” Hij voegt eraan toe: “De logistieke puzzel wordt dus nog complexer, maar tegelijkertijd zien we het als een enorme kans om dit historische terrein toekomstbestendig te maken. We zijn voorlopig nog niet klaar.”
NIEUWSBRIEF
Bouwen aan de toekomst van Beemsterkaas
De Beemster
Gepubliceerd op 1 juli 2025
In het hart van de Beemsterpolder, omringd door werelderfgoed, ligt de kaasmakerij van CONO Kaasmakers. Hier, op deze historische grond, wordt de beroemde Beemsterkaas geproduceerd — een proces dat diepgeworteld is in traditie, maar tegelijkertijd blijft vernieuwen. Een recent voorbeeld van deze innovatie is de ingebouwde liftinstallatie in de poedermakerij en de aanleg van een nieuwe hygiënesluis, gerealiseerd in samenwerking tussen CONO en bouwbedrijf K_Dekker.
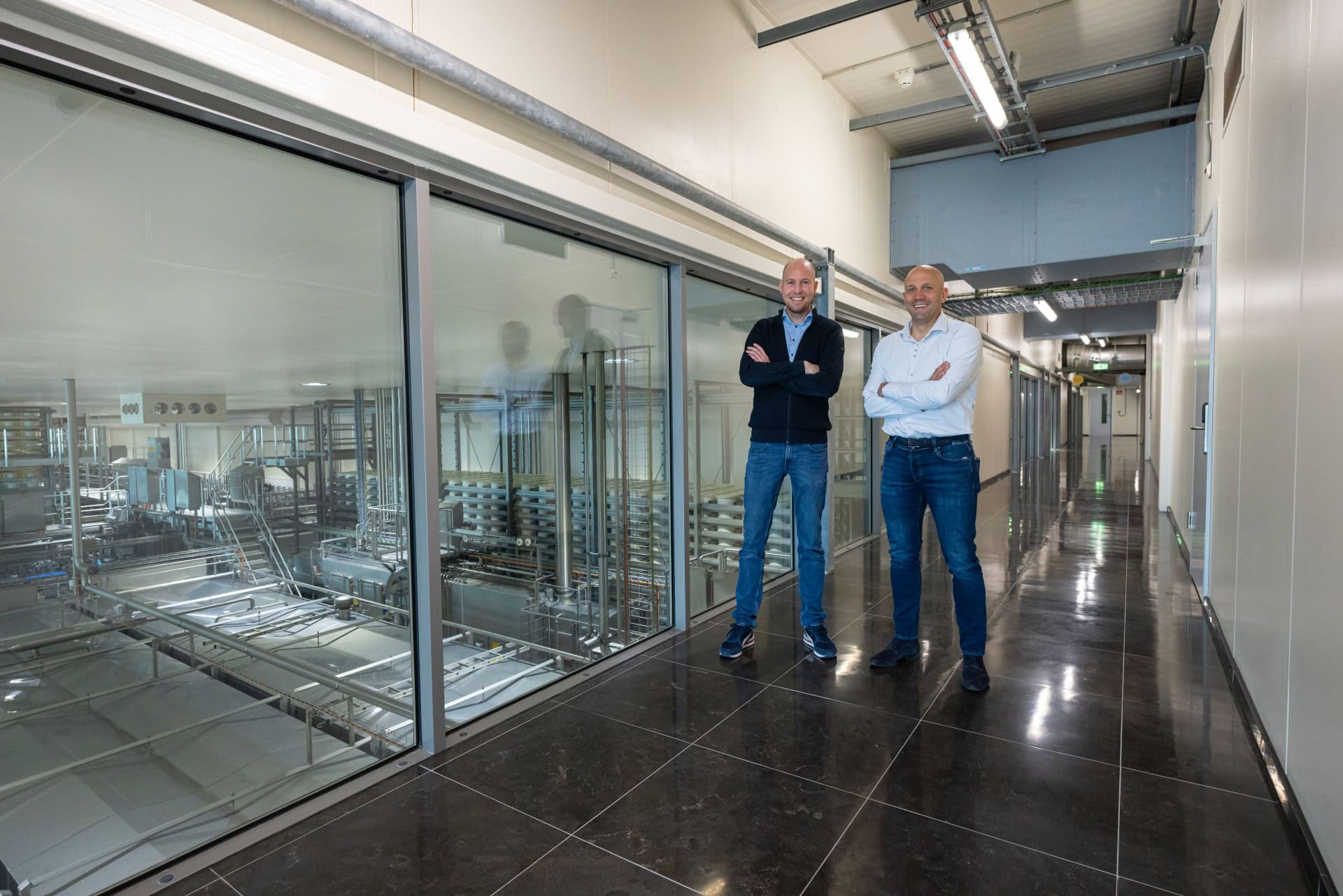
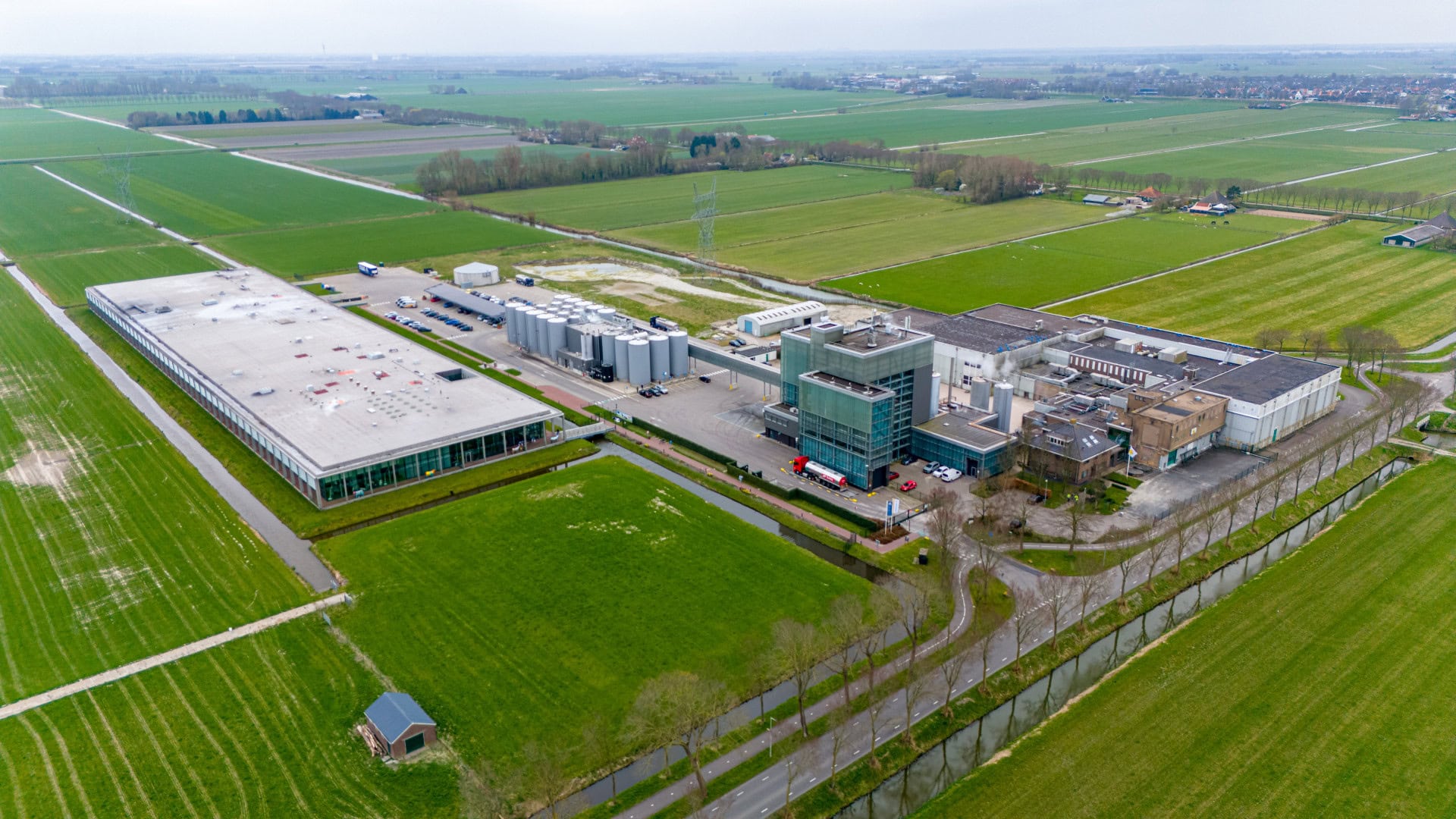
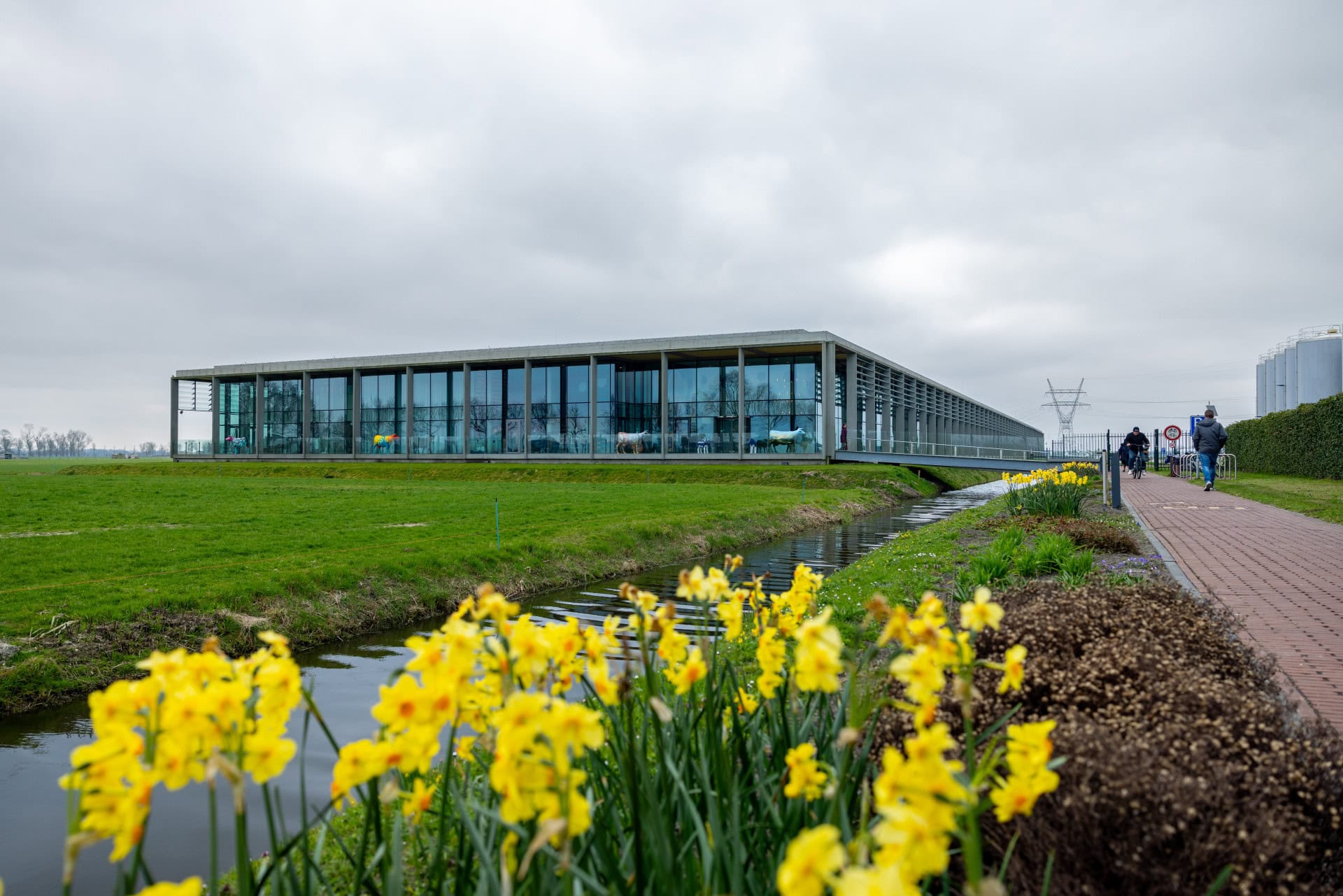
“Onze melkstroom is constant,” vertelt Tijs Roeland, Manager Techniek & Projecten bij CONO, terwijl hij langs imposante melkbuizen loopt. “Elke dag ontvangen we hier 1,1 miljoen liter melk. Koeien geven immers 24/7 melk, en wij kunnen simpelweg niet even stoppen. De productie moet dus altijd doorlopen, ook tijdens bouwprojecten. Stilstand is simpelweg geen optie.”
Rick Zutt, bedrijfsleider kleinbouw bij K_Dekker, onderstreept de bijzondere dynamiek van het project: “We zijn heel vroeg in het proces aangehaakt. Alles is prefab voorbereid om de bouwtijd op locatie zo kort mogelijk te houden. De lift moest midden in de productietoren komen, zonder dat we de productie stil konden leggen. Dat vergt een enorme mate van voorbereiding en precisie.”
De rol van de poedermakerij
De poedermakerij vormt een essentiële schakel binnen CONO. Hier wordt melk die niet direct tot kaas wordt verwerkt, zorgvuldig omgezet in melkpoeder, zodat elke liter optimaal benut wordt. “De fallback-optie,” noemt Tijs het met een glimlach. “En ook die poeder is een waardevol product dat we actief in de markt zetten.”
Het proces vraagt om uiterste precisie: de melk wordt eerst gezuiverd, vervolgens geconcentreerd en uiteindelijk gedroogd tot poeder. Dit poeder wordt ingezet voor uiteenlopende toepassingen. Tijs legt uit: “Het stelt ons in staat om flexibel te zijn in de markt en maximale waarde te halen uit onze melkstromen. Geen druppel gaat verloren.” De poedermakerij draait continu, net als de rest van de fabriek, en is daarmee een onmisbare schakel in het streven van CONO naar volledige benutting en duurzaamheid van hun producten.
Techniek en voorbereiding: de nieuwe liftinstallatie
Om de liftinstallatie succesvol te integreren, werd de bouwplek zorgvuldig afgeschermd met robuuste stalen frames en luchtdichte folies. Zelfs het bestaande noodtrappenhuis moest tijdelijk worden vervangen. “Veiligheid staat hier altijd op de eerste plaats,” benadrukt Tijs. “We werken met strikte hygiëne-eisen en elke stap moet minutieus worden gepland en uitgevoerd, elke dag opnieuw.”
Van buitenaf oogt de kaasmakerij bescheiden, maar schijn bedriegt: ondergronds strekt het complex zich uit tot wel tien meter diepte. “Onze fabriek is eigenlijk binnenstebuiten gebouwd,” glimlacht Tijs. “Waar je normaal naar boven bouwt, zijn wij de grond in gegaan. Dat maakt het werk uitdagender, maar biedt tegelijkertijd unieke voordelen op het gebied van temperatuurbeheersing en duurzaamheid.”
Een groot deel van de operatie draaide om uiterste precisie en doordachte voorbereiding. “We hebben een volledige 3D-scan van de ruimte gemaakt,” vertelt Rick. “Alles moest tot op de millimeter kloppen. Als de liftinstallatie niet had gepast, zaten we met een immens probleem. Daarom is alles in 3D ontworpen en in de fabriek geprefabriceerd.” Met een kraan werden het trappenhuis en de liftinstallatie uiteindelijk via een speciaal geopend dakdeel naar binnen gehesen. Binnen zes weken was de klus geklaard, zonder ook maar één dag productieverlies.
Flexibiliteit en samenwerking
Naast de lift werkte K_Dekker ook intensief mee aan de vernieuwing van de kristallisatietanks. Deze tanks spelen een cruciale rol in het proces waarbij restproducten uit de kaasproductie verder worden verwaard. “We werken steeds vaker met tijdelijke productieschema’s,” licht Tijs toe. “Dan produceren we bijvoorbeeld vloeibare producten in plaats van poeder om renovatiewerkzaamheden mogelijk te maken. Dit vergt een enorme flexibiliteit van onze medewerkers.”
De samenwerking tussen CONO en K_Dekker wordt gekenmerkt door een gedeelde visie op duurzaamheid, veiligheid en transparantie. “Niet iedere aannemer kan zomaar binnen deze muren werken,” benadrukt Tijs. “Je moet begrijpen hoe kritisch voedselveiligheid hier is. Iedere handeling telt mee.”
Vooruitblik: elektrificatie
De blik is echter ook stevig op de toekomst gericht. Zo werkt CONO momenteel aan een volledige elektrificatie van de fabriek. “We gebruiken nu nog veel stoom,” legt Tijs uit, terwijl hij wijst naar de immense installaties. “Maar met onze nieuwe, versterkte stroomaansluiting kunnen we straks alles via warmtepompen en elektrische boilers doen. Daarmee zetten we een enorme stap richting CO2-reductie.”
Door restwarmte slim terug te winnen, wordt bovendien veel energie bespaard. “En het mooiste is,” lacht Tijs trots, “de smaak en kwaliteit van onze Beemsterkaas blijven exact hetzelfde. Daar doen we geen enkele concessie aan. De consument zal niets merken, behalve dan dat onze kaas nog duurzamer geproduceerd wordt.”
Vakmanschap en samenwerking
Wat is het geheim van CONO? Tijs hoeft niet lang na te denken: “Nuchterheid, vakmanschap en nooit concessies doen aan kwaliteit. We werken met passie en respect voor ons product. En dat proef je terug in iedere hap Beemsterkaas.”
De samenwerking met K_Dekker geldt inmiddels als een schoolvoorbeeld van hoe moderne bouwprojecten in complexe voedselomgevingen kunnen slagen. Rick vat het treffend samen: “Als je elkaar snel weet te vinden, problemen direct benoemt en samen zoekt naar oplossingen, kun je samen echt hele mooie dingen bouwen. Dat is waar ons partnerschap op gestoeld is, en dat zie je terug in de samenwerking.”
NIEUWSBRIEF
Nieuwe toekomstgerichte fabriek bij RAVO
Alkmaar
Gepubliceerd op 1 juli 2025
Op een bruisend bedrijventerrein in Alkmaar, midden in een bedrijvige regio vol innovatieve maakindustrie, staat de fabriek van RAVO – een gerenommeerde fabrikant van veegmachines en onderdeel van de internationaal opererende FAYAT Groep. Dagelijks rollen hier drie spiksplinternieuwe, state-of-the-art veegmachines van de band, stuk voor stuk met trots geproduceerd in Nederland. Recent onderging een nieuw aangekocht fabriekspand op hetzelfde terrein een grondige metamorfose. K_Dekker kleinbouw transformeerde het gebouw tot een ultramoderne testwerkplaats, een opleidingscentrum en nieuwe kantoorruimten, met bijzondere aandacht voor duurzaamheid en hergebruik van materialen.
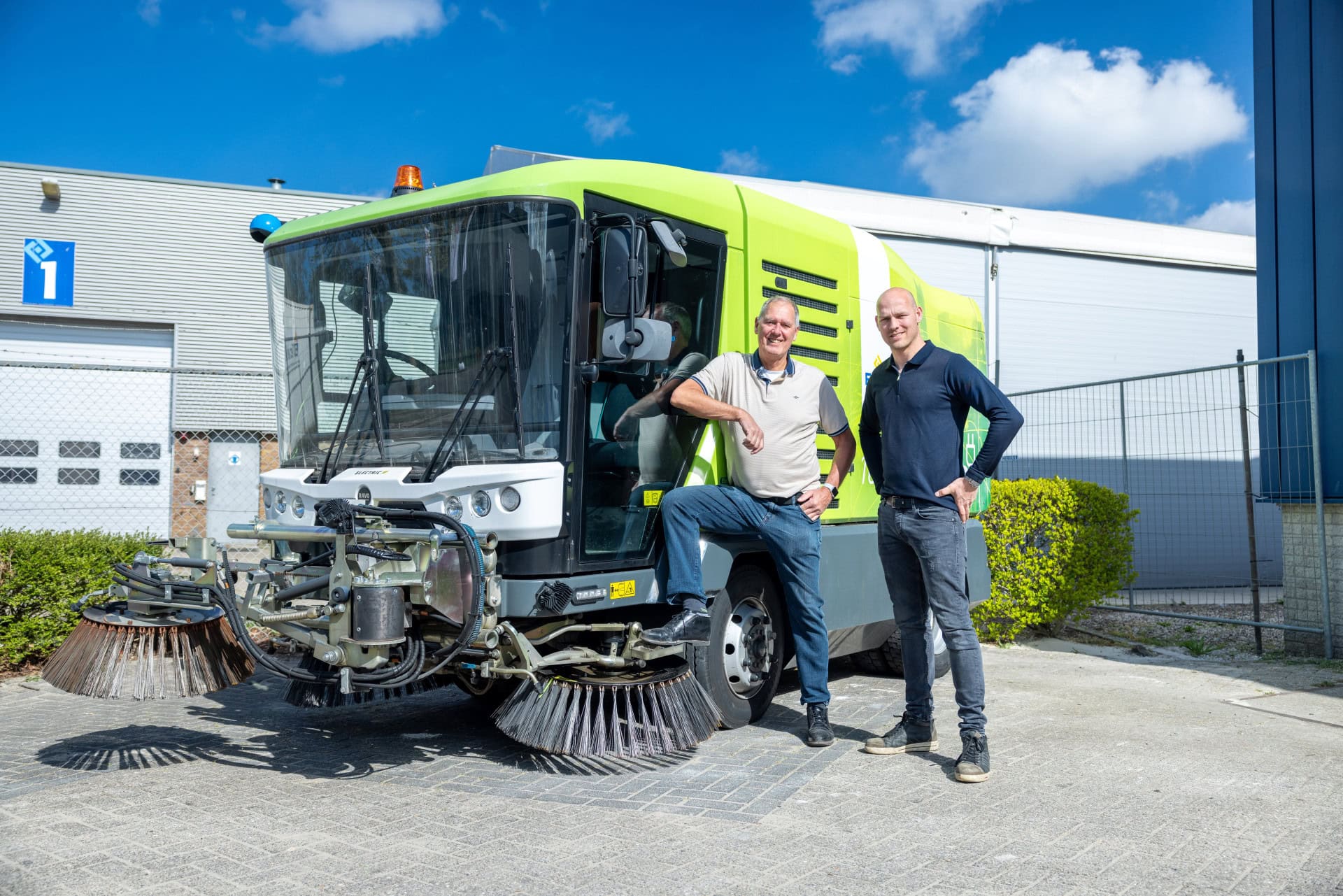
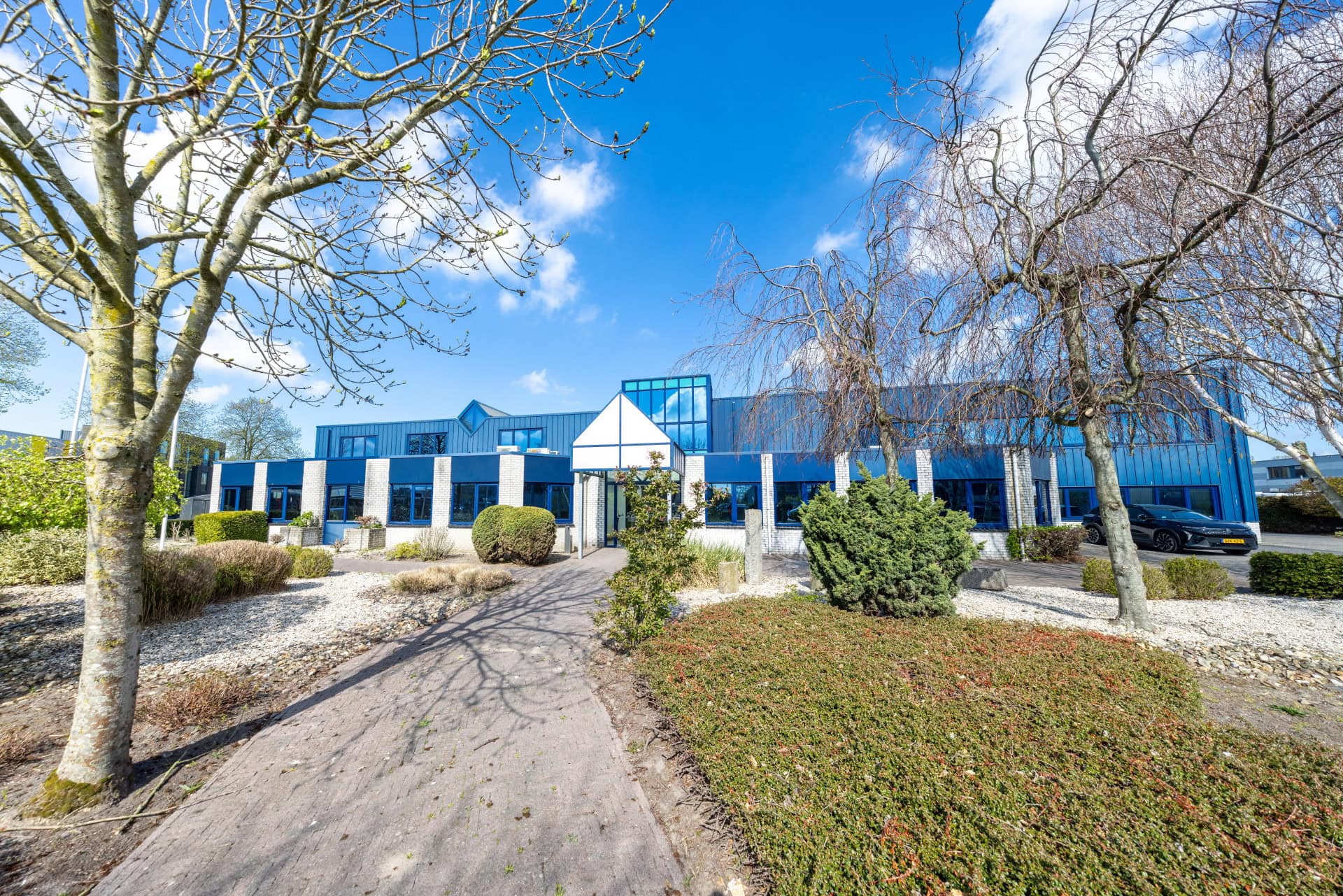
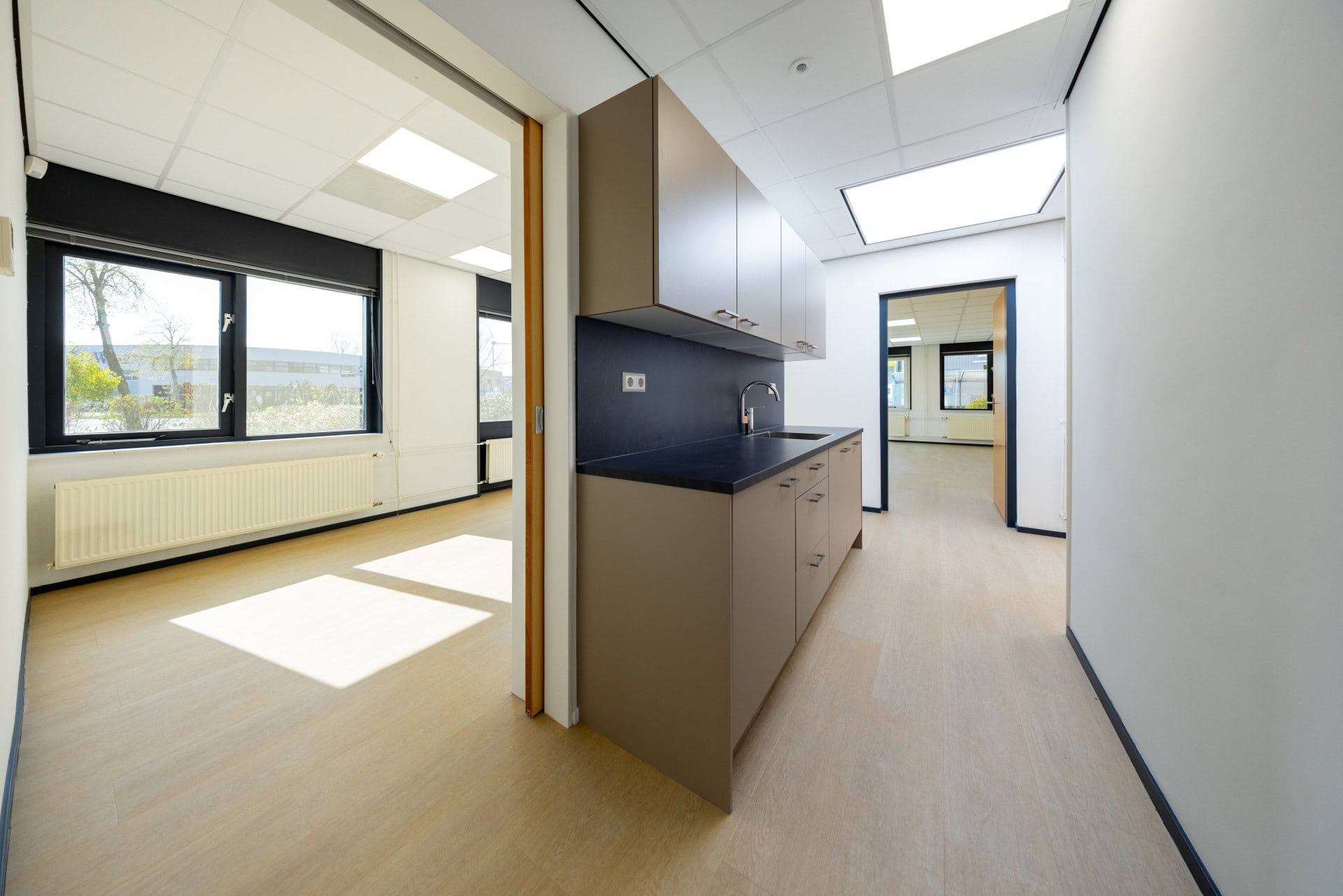
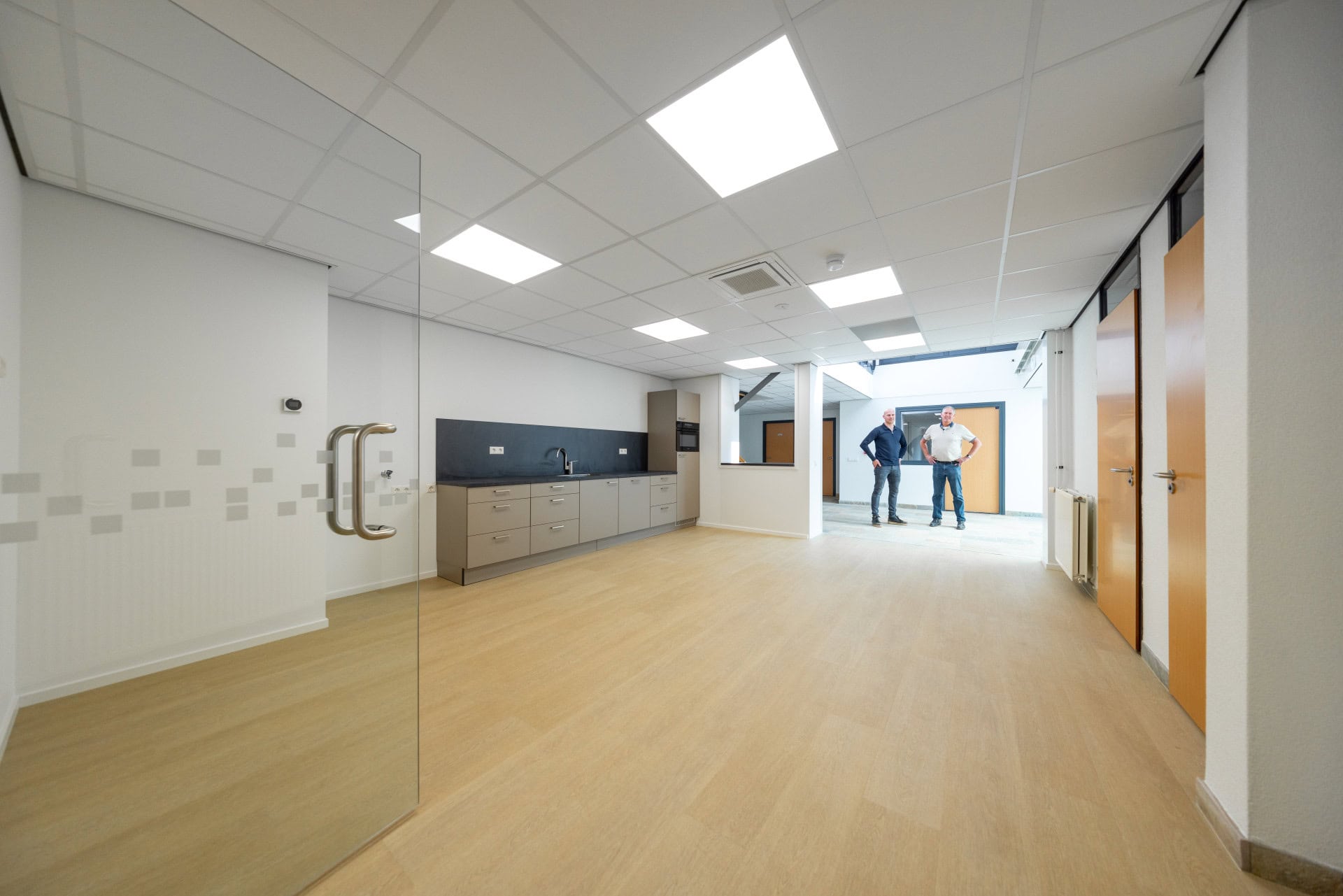
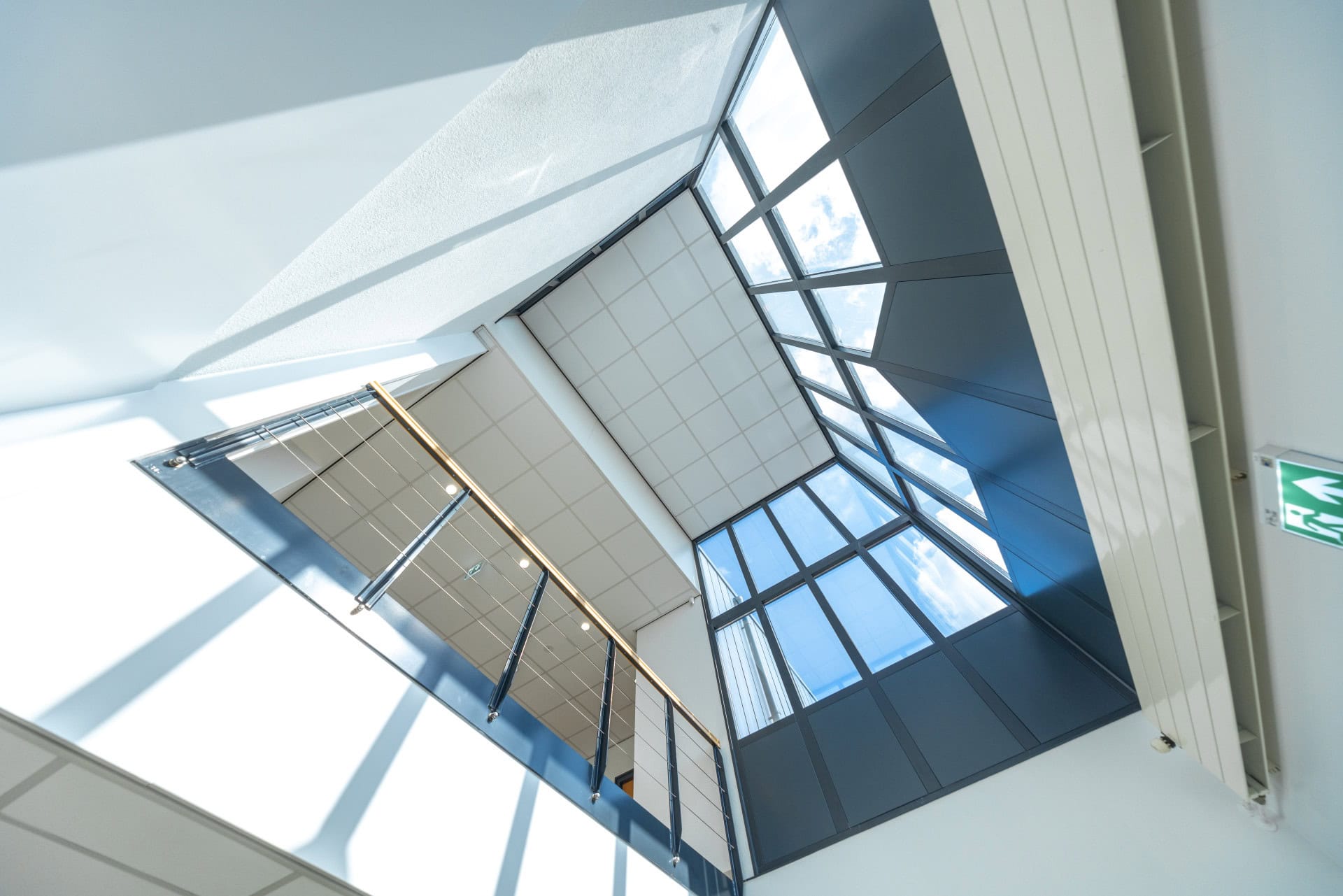
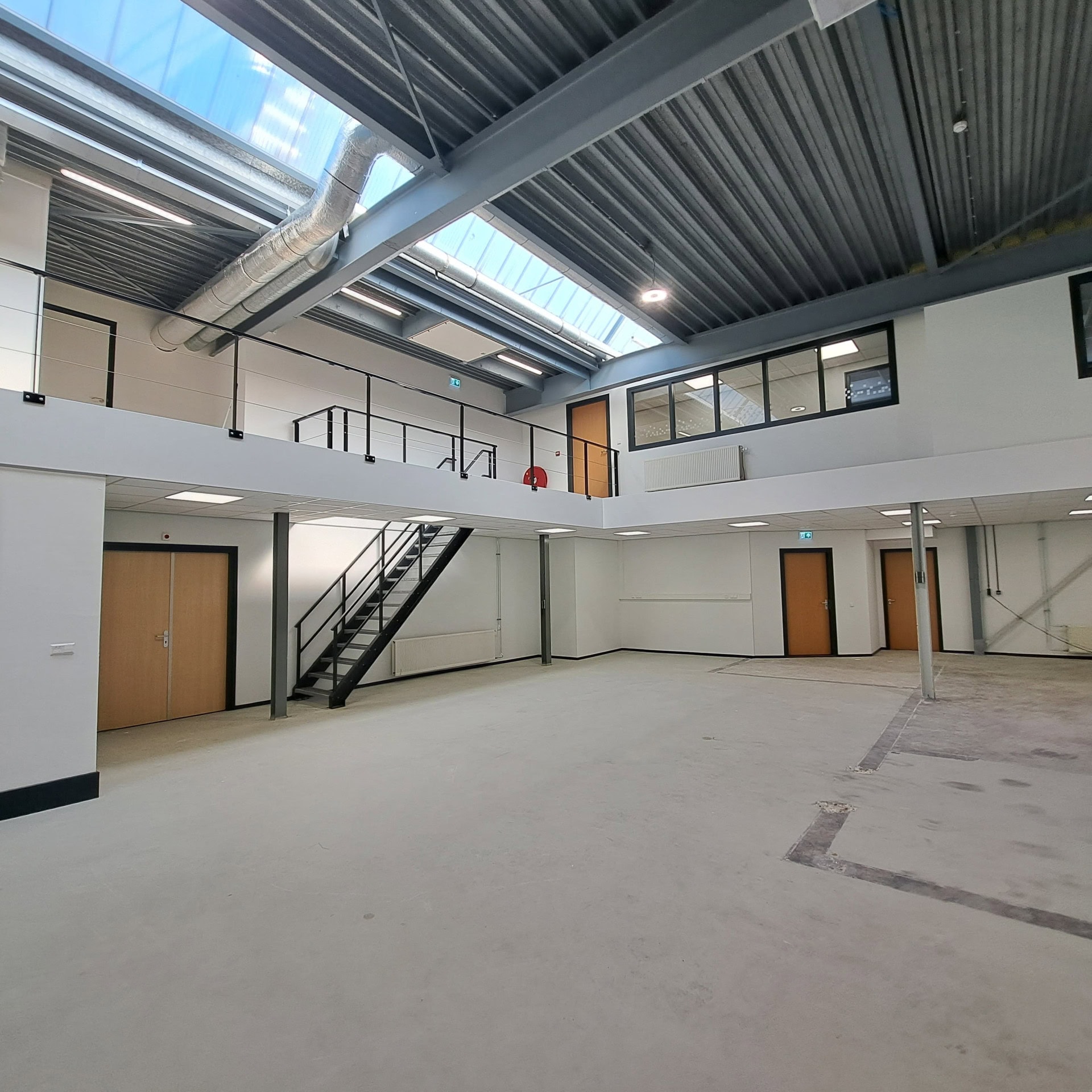
Projectleider Operations John van der Lans van RAVO licht toe: “We wilden graag onze verschillende locaties centraliseren. We zaten verspreid over vijf locaties, wat een uitdaging was voor communicatie en logistiek.” Daarom werd gekozen voor een slimme verbouwing van een recent aangekochte locatie: “Met dit masterplan konden we onze afdelingen centraliseren en synergie creëren tussen de teams,” aldus John.
Het nieuwe pand wordt een essentieel centrum voor de aftersales-afdeling, die wereldwijd onderdelen levert en onderhouds- en storingsdiensten verzorgt. “Hier geven we bovendien trainingen aan dealers en eindgebruikers,” vervolgt John. Door de directe nabijheid van de R&D-afdeling kunnen innovaties en wijzigingen in ontwerp direct vertaald worden naar praktische trainingen: “Deze integratie is nu aanzienlijk efficiënter.”
Kiezen voor duurzaamheid: de circulaire visie van K_Dekker
Bij de keuze voor een bouwpartner werd John geïnspireerd door K_Dekkers circulaire aanpak. “Een specifiek voorbeeld sprak me aan: een school met een beperkt budget waarbij ouders en docenten zelf materialen verwijderden voor hergebruik. K_Dekker realiseerde vervolgens de verbouwing met deze materialen. Dat vond ik een aantrekkelijke en duurzame manier van werken,” vertelt hij enthousiast.
Pascal van der Geest, projectbegeleider bij K_Dekker kleinbouw, benadrukt het persoonlijke en flexibele karakter van dit project. “Ik werk inmiddels 14 jaar bij K_Dekker en merk dat projecten zoals deze, waar persoonlijk contact en intensieve samenwerking centraal staan, goed passen bij mijn werkstijl.”
Snelle start dankzij wederzijds vertrouwen
John prijst de soepele samenwerking met K_Dekker: “Vanaf het eerste contact werkte K_Dekker met vertrouwen en enthousiasme. Zelfs voordat de investering officieel goedgekeurd was, begonnen we met de werkvoorbereiding.” Deze proactieve benadering bleek succesvol: “Toen het groene licht kwam, konden we binnen drie weken met de uitvoering starten. Dat was indrukwekkend snel.”
Creatief hergebruik en slimme oplossingen tijdens de verbouwing
De uitvoering verliep voorspoedig en creatief, met oog voor detail en duurzaamheid. Diverse bestaande materialen zoals radiatoren, deuren en kozijnen werden zorgvuldig gedemonteerd en elders in het project hergebruikt. “Het hergebruik van goede materialen bespaart aanzienlijk op kosten en sluit perfect aan bij onze visie op duurzaamheid,” aldus John.
Tijdens het bouwproces ontstonden ook onverwachte uitdagingen, zoals verborgen constructieve elementen die aanvankelijk niet bekend waren. “We kwamen bijvoorbeeld stalen balken en kruisverbanden tegen, die niet eenvoudig te verwijderen waren,” vertelt Pascal. “Dankzij snel schakelen en goed overleg tussen architecten, onze eigen constructie-experts en het team van RAVO konden we deze hindernissen zonder vertraging oplossen.”
John vult aan: “We waren enorm onder de indruk van hoe flexibel K_Dekker hiermee omging. Problemen werden vaak nog dezelfde dag aangepakt en opgelost. Dat gaf ons enorm veel vertrouwen.” Volgens beide mannen was de efficiënte communicatie essentieel voor het succes van dit project. “Het intensieve overleg en de korte lijnen maakten deze verbouwing bijzonder prettig,” zegt Pascal.
Meer werkplezier en betrokkenheid dankzij slim ontwerp
De nieuwe faciliteit biedt niet alleen praktische voordelen, maar verhoogt ook het werkplezier van de medewerkers. Grote ramen op de eerste verdieping, geplaatst in hergebruikte kozijnen, bieden uitzicht op de productiehal beneden, waar recentelijk een uiterst strakke en gladde vloer is gelegd. Dit verhoogt de betrokkenheid van het personeel aanzienlijk. John glimlacht: “Uiteindelijk doe je het voor de mensen die hier werken. Het is geweldig om te zien hoe enthousiast ze reageren.” John kijkt alvast vooruit naar een volgende uitdaging: “Door de groeiende vraag naar elektrische veegmachines zullen we binnenkort ook onze hoofdproductiehal grondig moeten verbouwen. Dat brengt weer nieuwe kansen én uitdagingen met zich mee. Gezien onze eerdere ervaringen kiezen we opnieuw graag voor K_Dekker als betrouwbare partner in dit traject. Hun aanpak sluit naadloos aan bij onze visie en ambities voor de toekomst.”
Samen trots op een succesvolle samenwerking
Zowel Pascal als John kijken met veel trots terug op het gezamenlijke traject en het behaalde resultaat. Pascal besluit tevreden: “Dit was écht een voorbeeldproject, waar vertrouwen, openheid en flexibiliteit centraal stonden. Precies zoals wij graag werken.” John beaamt: “De Westfriese mentaliteit van aanpakken, duidelijkheid en doen wat je belooft, paste perfect bij ons bedrijf. Geen lange verhalen, maar resultaat.”
NIEUWSBRIEF
Uitbreiding drinkwatercapaciteit in Heemskerk
Heemskerk
Gepubliceerd op 1 juli 2025
De Combinatie Zuiver Bouwen (CZB), een unieke samenwerking tussen bouwbedrijven K_Dekker en GMB, staat centraal bij de grote capaciteitsuitbreiding van de drinkwaterproductie van PWN in Heemskerk. Dit omvangrijke project, dat de toekomstige drinkwatervoorziening in Noord-Holland robuuster moet maken, kent een breed scala aan uitdagingen en vereist een intensieve samenwerking tussen alle betrokken partijen.
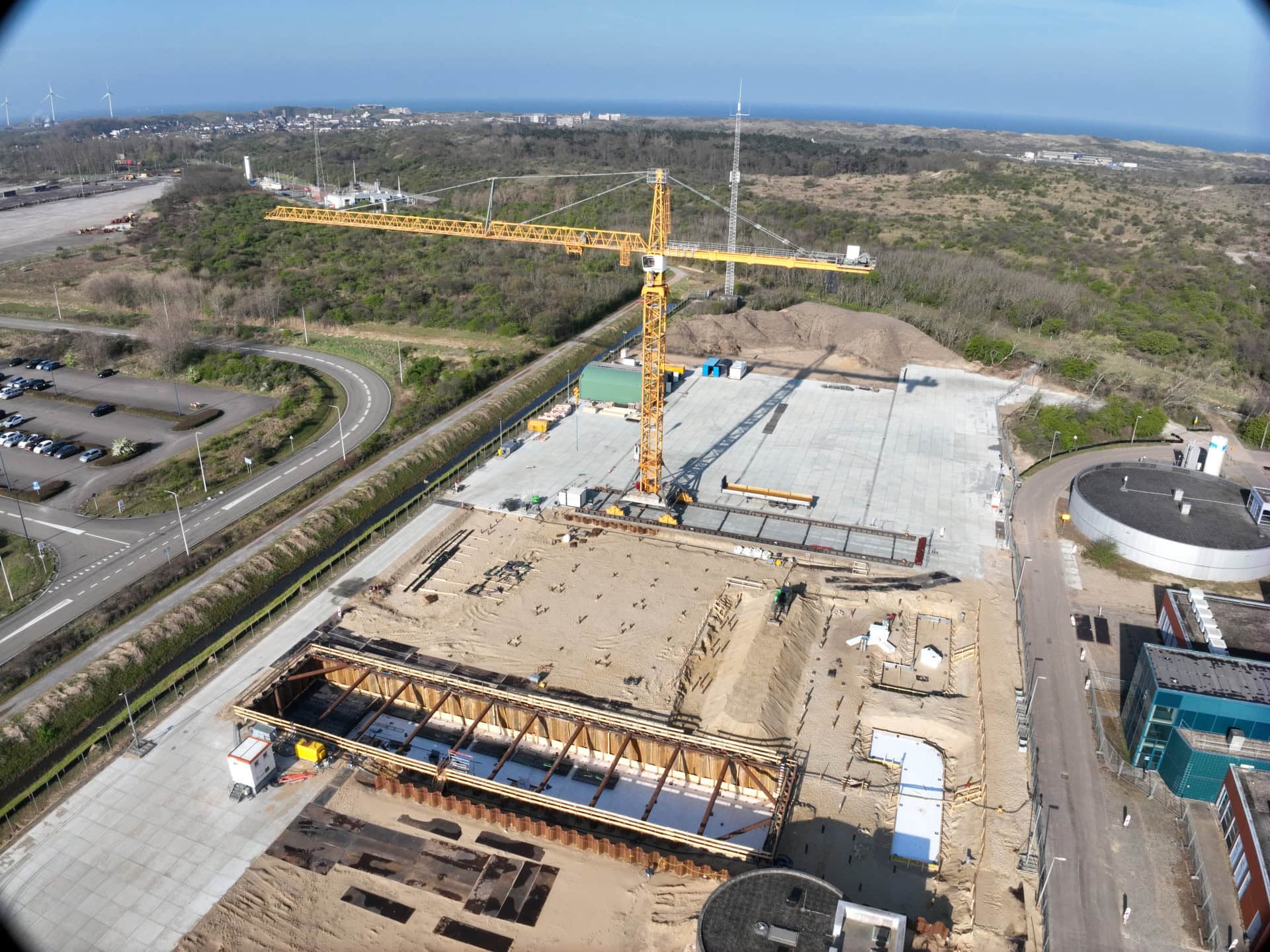
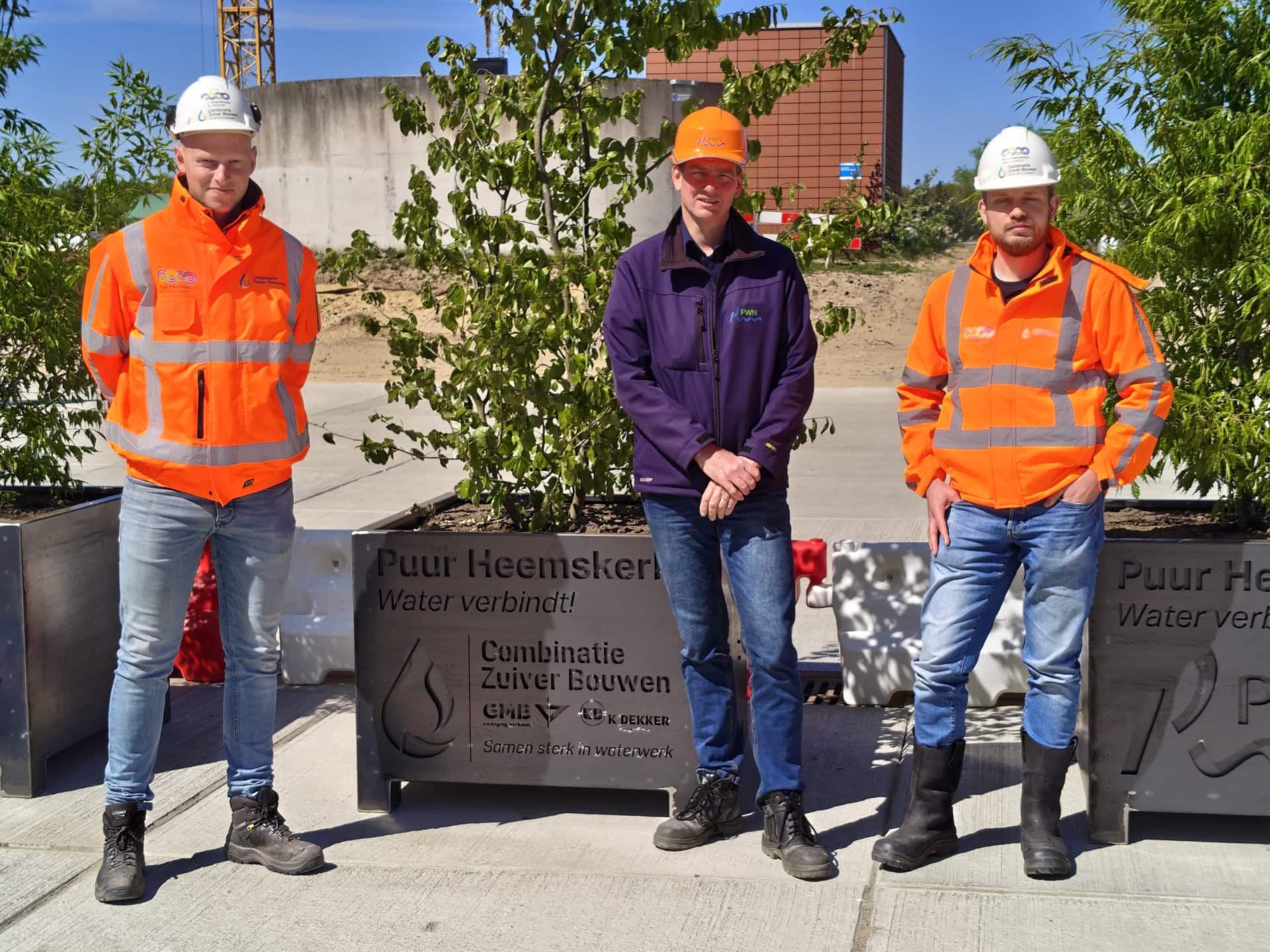
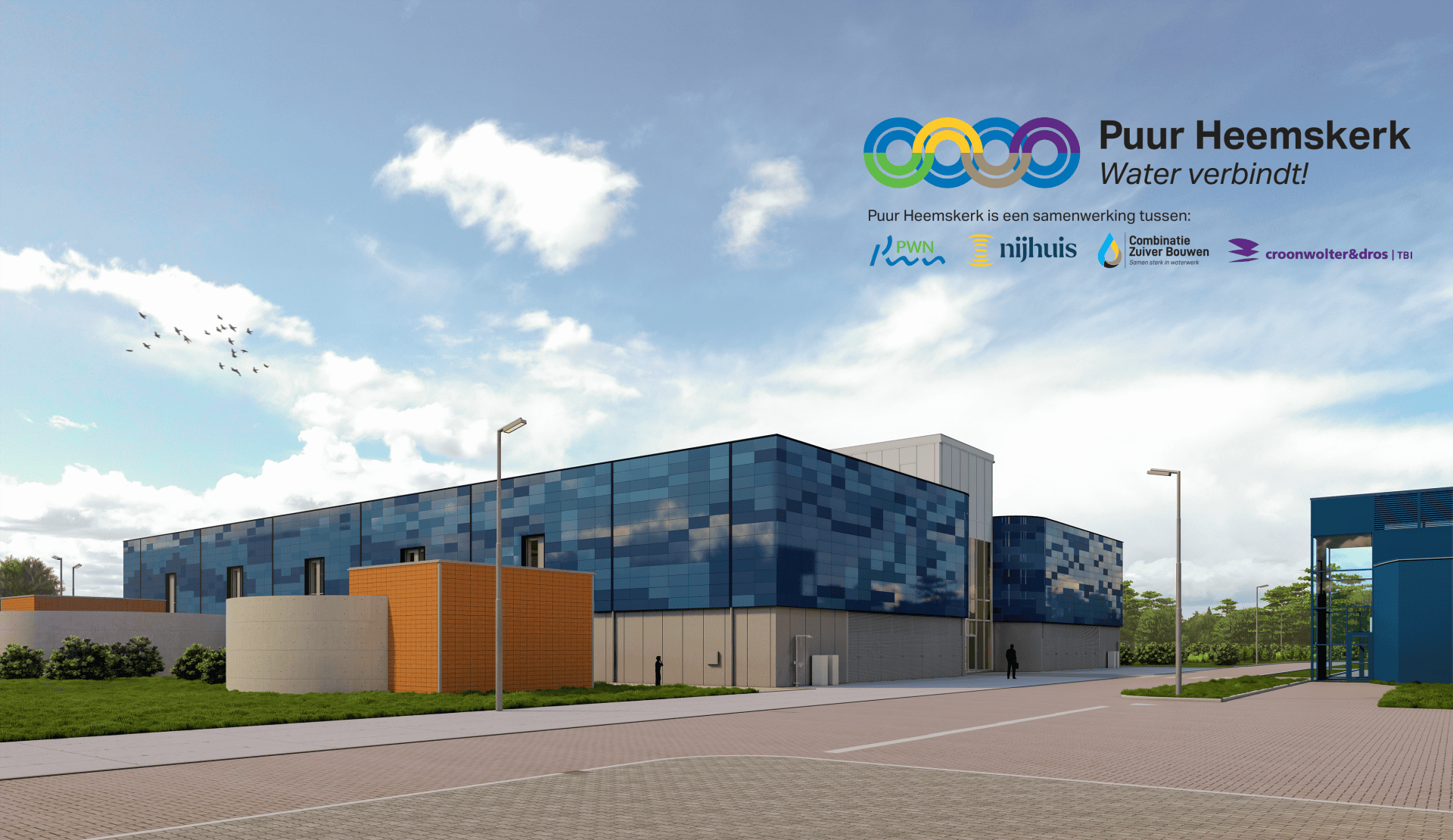
“Onze combinatie is ontstaan omdat we elkaar uitstekend aanvullen,” vertelt Maarten Gaasenbeek, procesmanager bij GMB en CZB. “GMB heeft veel expertise in werktuigbouwkunde en ondergrondse leidingen, terwijl K_Dekker sterk is in bouwkunde. Beide bedrijven zijn ervaren betonbouwers. Die technische complementariteit maakt onze samenwerking sterk.”
Gijs Korver, uitvoerder bij K_Dekker en betrokken bij CZB, benadrukt hoe de samenwerking verder wordt versterkt door de overeenkomstige bedrijfsculturen van beide familiebedrijven. “We begrijpen elkaar goed, hebben vergelijkbare normen en waarden en kennen dezelfde no-nonsense mentaliteit. Dat helpt enorm tijdens zo’n omvangrijk en complex project.”
De bouwcombinatie voert de civiele en bouwkundige werkzaamheden uit en verzorgt de aanleg van procesleidingen. Daarbij werkt CZB nauw samen met Nijhuis Saur Industries, verantwoordelijk voor werktuigbouwkundige installaties, en Croonwolter & Dros, dat zich bezighoudt met elektrotechnische aspecten. Deze partijen vormen samen Bouwcombinatie Puur Heemskerk, maar opereren wel onder eigen contracten voor opdrachtgever PWN.
Een van de grootste uitdagingen bij dit project is dat de werkzaamheden plaatsvinden terwijl de bestaande waterproductie moet blijven draaien. “De winkel moet open blijven,” verduidelijkt Simon de Wit, bedrijfsvoerder bij PWN. “We hebben een strakke planning en coördinatie nodig zodat bestaande productieprocessen van PWN minimaal worden verstoord.”
Simon benoemt ook een andere technische uitdaging: “Het hele bouwproces moet emissieloos worden uitgevoerd. Speciaal voor deze stroomvraag zijn de diverse bouwstroomaansluitingen in het terrein zorgvuldig bekeken en extra zwaar uitgevoerd, wat een enorme logistieke operatie was.”
Emissieloos
Deze elektrificatie bracht aanvankelijk de nodige vragen en onzekerheden met zich mee, erkent Maarten. Hij zegt hierover: “In het bouwteam vonden we het spannend, aangezien zowel PWN als wijzelf nog beperkt ervaring hadden met volledig emissievrij werken op deze schaal. Gelukkig zien we nu dat het goed werkt.”
Een ander kritiek punt is de tijdelijke ombouw van de ontvangstkelder van het complex, waardoor het team op korte termijn intensieve werkzaamheden moet uitvoeren zonder de productiecapaciteit in gevaar te brengen. “Voor de werkzaamheden is een tijdelijke bypass in het leidingwerk gerealiseerd. Op die wijze is het mogelijk de kelder buiten dienst te nemen. Dan kunnen we in een beperkt tijdspan de werkzaamheden in de ontvangstkelder uitvoeren,” legt Gijs uit. “Maar natuurlijk blijft er altijd enige spanning totdat het systeem volledig operationeel en bewezen effectief is.”
CZB heeft bewust gekozen voor een eigen identiteit binnen dit project. Maarten legt uit: “We hebben onze eigen naam, Combinatie Zuiver Bouwen, gecreëerd om te benadrukken dat we één geïntegreerd team zijn. Dat wordt door onze opdrachtgever ook sterk gewaardeerd.”
“Je merkt niet wie bij welk bedrijf hoort, iedereen spreekt met één stem,” bevestigt Simon. “Die eenheid is cruciaal voor het succes van zo’n complex bouwproject.”
De recente mijlpalen zoals de eerste succesvolle procesleiding-aanpassingen en de symbolische start van de nieuwbouw, die werd bijgewoond door prominenten uit provincie en gemeente, tonen aan hoe essentieel en succesvol deze integrale aanpak is. “Iedereen beseft dat we hier iets bouwen dat cruciaal is voor de toekomst van onze regio,” concludeert Gijs.
Met deze nauwe samenwerking zet CZB samen met PWN een belangrijke stap naar een duurzame, betrouwbare en toekomstbestendige drinkwatervoorziening in Noord-Holland.
Gezien het succes en de positieve ervaring van alle betrokken partijen ligt het in de verwachting dat de samenwerking binnen de Combinatie Zuiver Bouwen in de toekomst zal worden voortgezet bij nieuwe projecten. “De synergie tussen K_Dekker en GMB is bewezen en smaakt absoluut naar meer,” besluit Maarten optimistisch.
NIEUWSBRIEF
Nieuw was- en zandvulgebouw voor GVB Amsterdam
Nieuwbouw was- en zandvulgebouw GVB
Gepubliceerd op 27 augustus 2024
In de uitgestrekte Legmeerpolder verrijst een bijzonder bouwproject, essentieel voor het functioneren van de nieuwe Uithoornlijn: het nieuwe was- en zandvulgebouw voor het GVB. Het gebouw, dat alle gekoppelde trams van de Uithoornlijn gaat bedienen, komt met unieke uitdagingen en oplossingen, vertellen Brenda Tesselaar, werkvoorbereider bij K_Dekker bouw & infra, en Jasper Hooijmans, Projectmanager Techniek bij GVB Amsterdam.
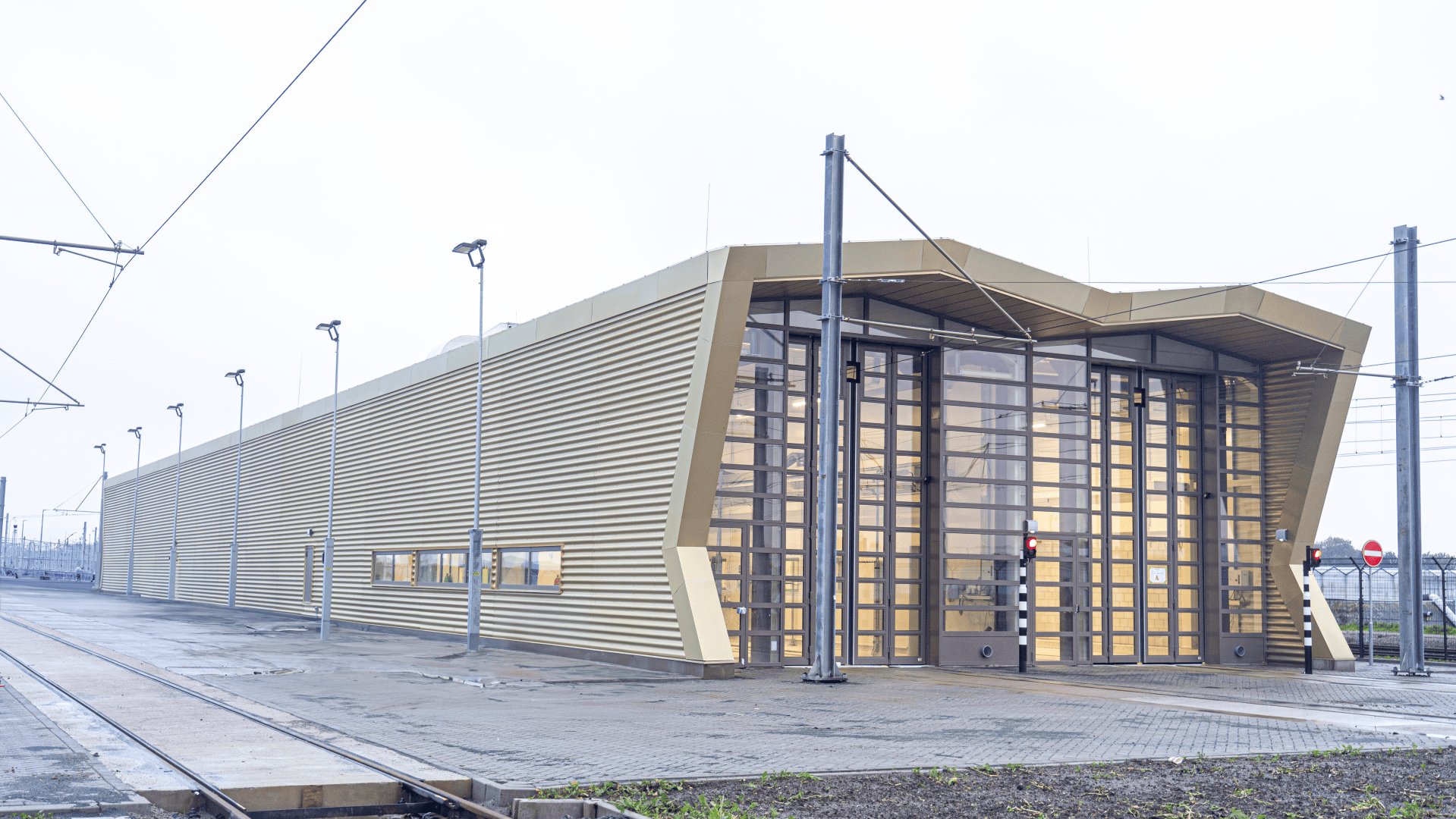
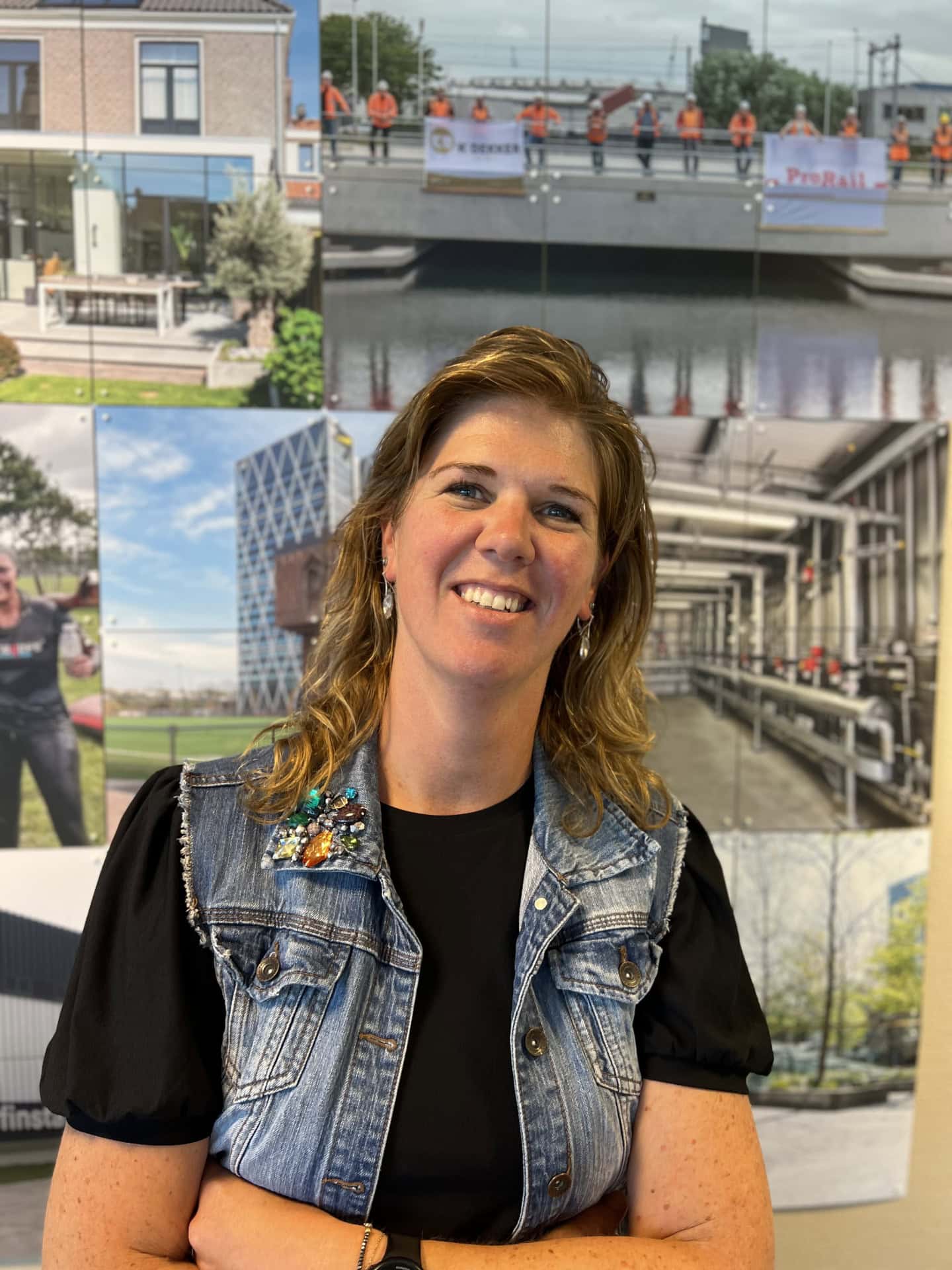
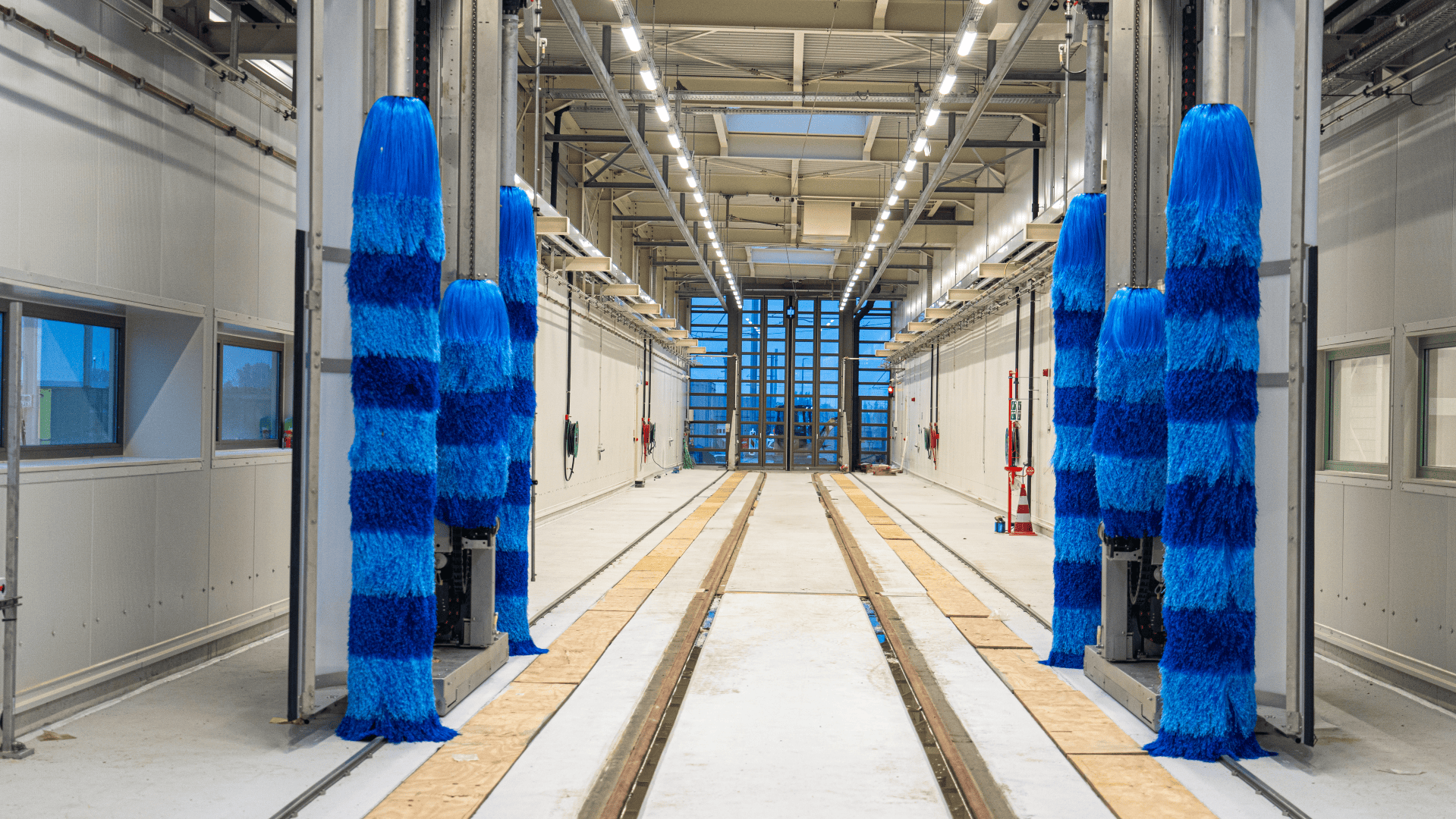
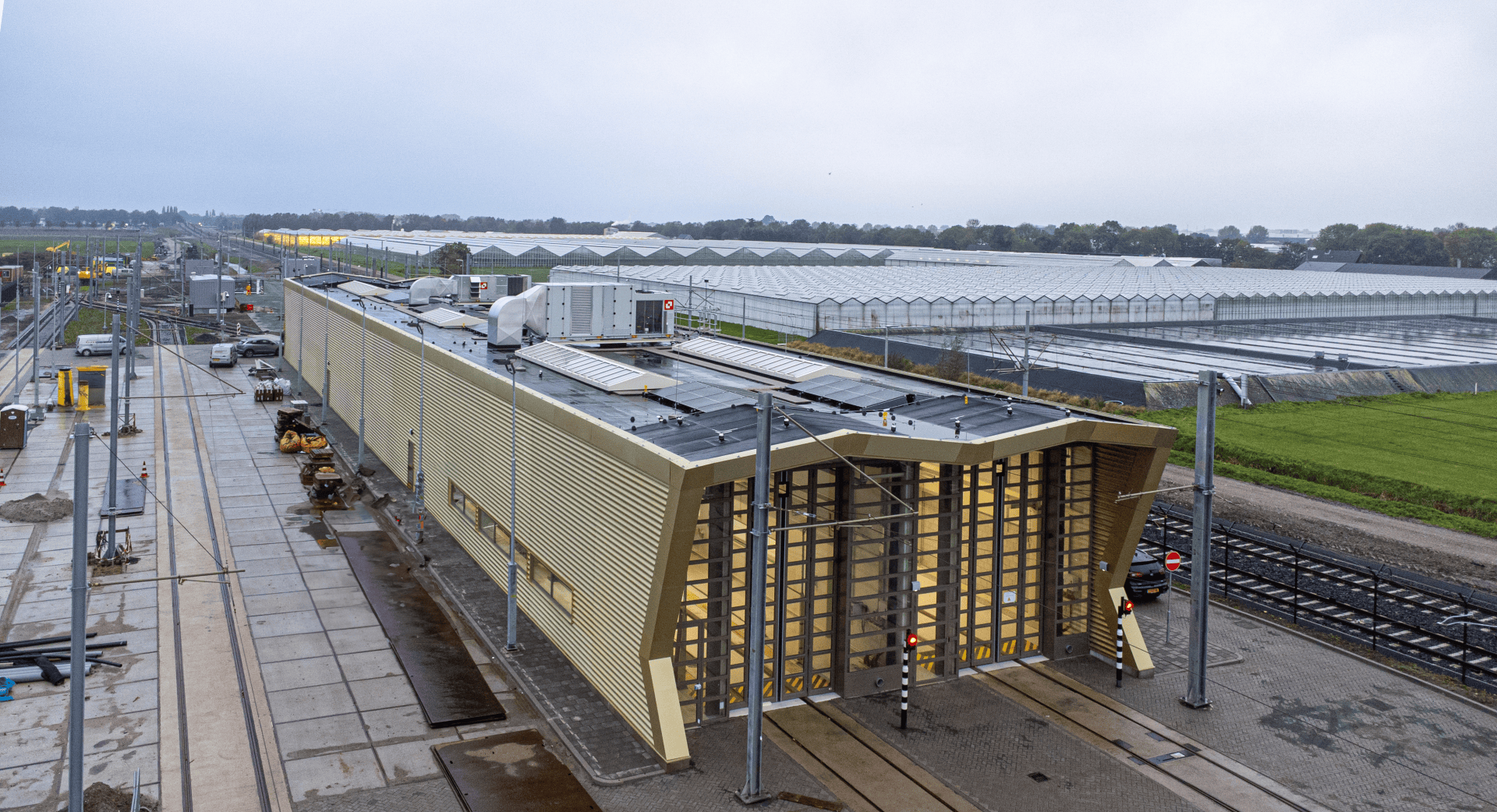
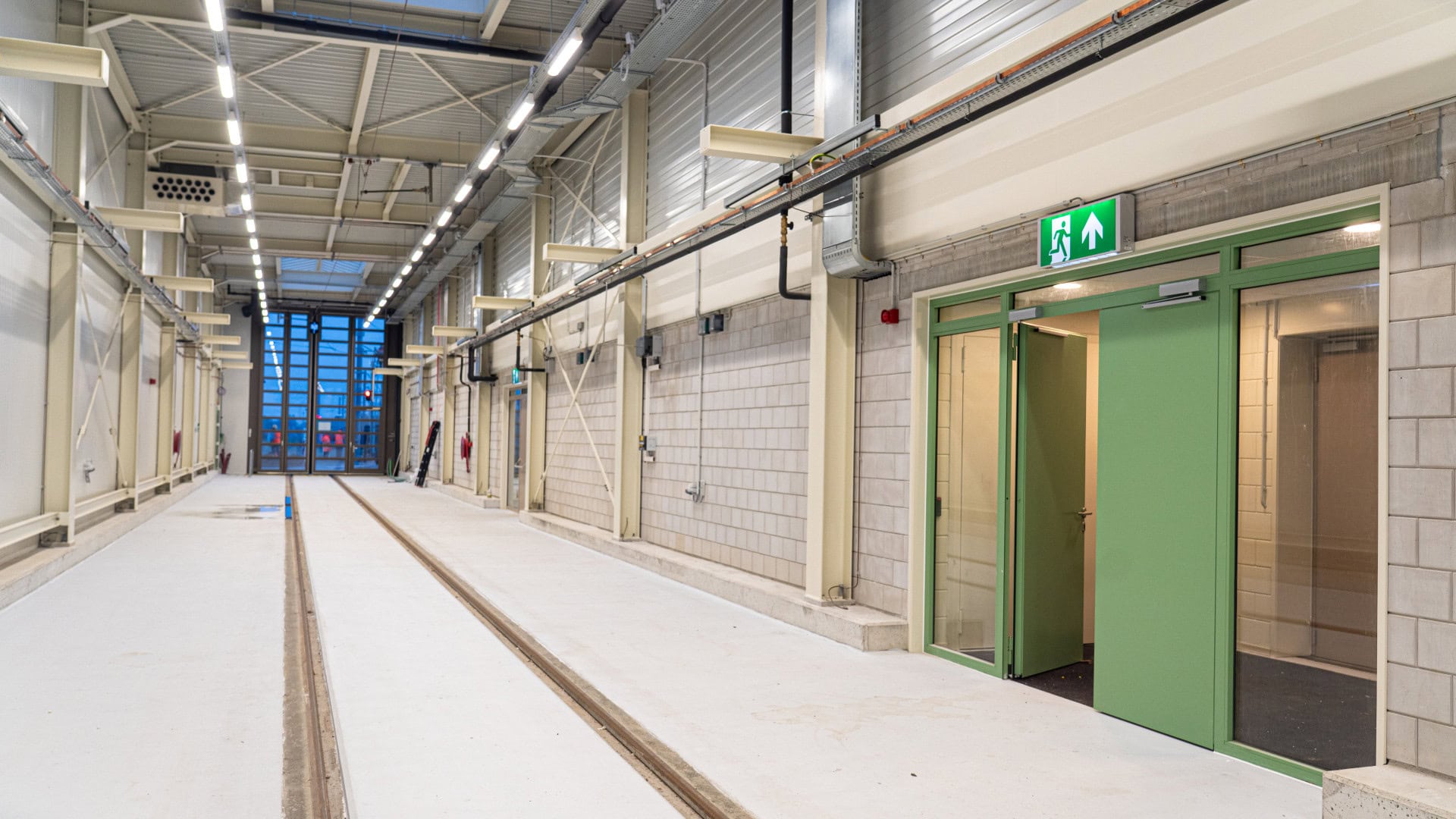
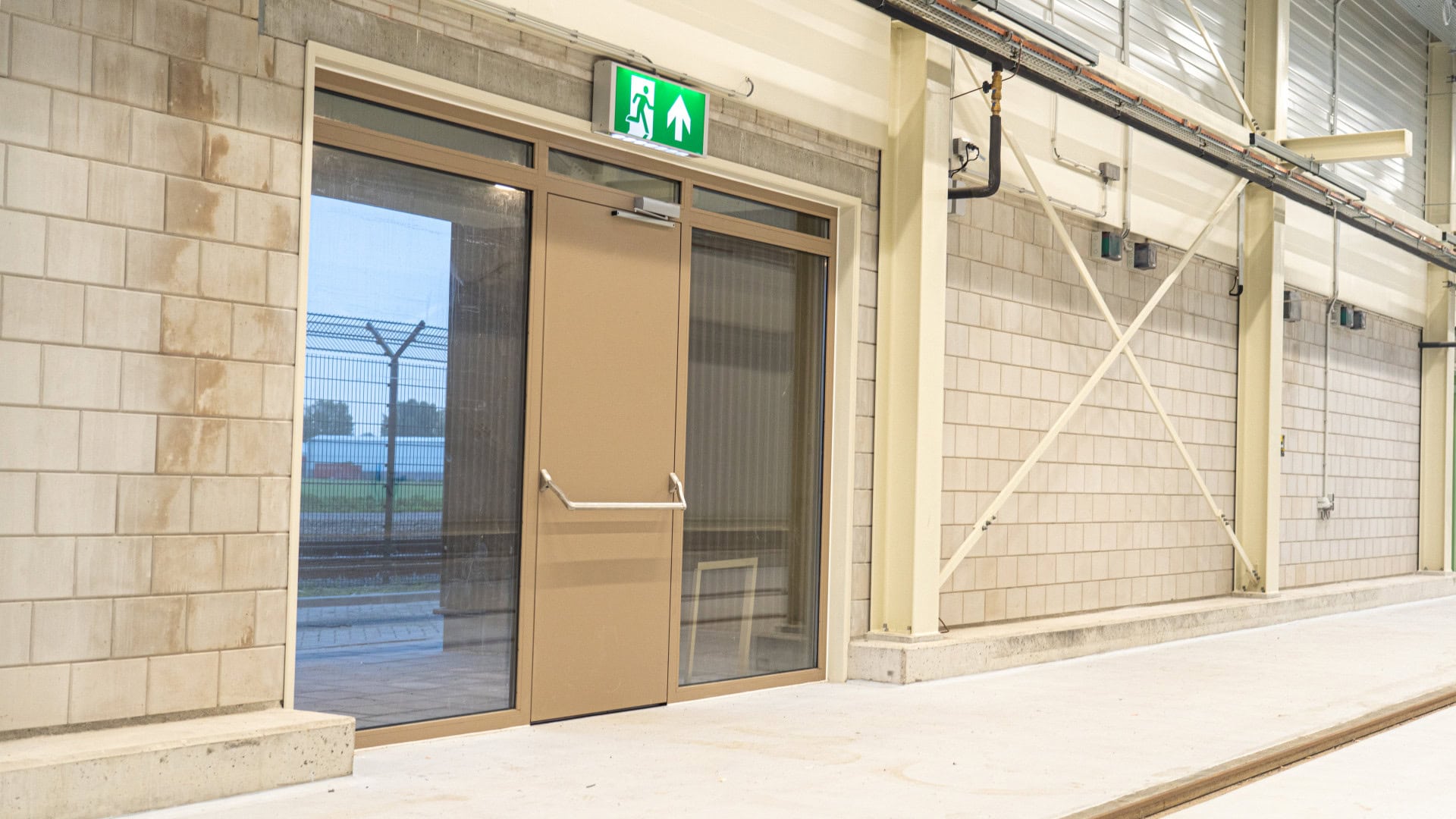
Het project betreft niet alleen een wasstraat voor trams maar ook een faciliteit voor het bijvullen van zand, wat essentieel is voor de remcapaciteit van de trams. De bouw van het project was niet zonder hobbels. “We hadden te maken met meerdere nevenaannemers en een complexe installatie,” deelt Tesselaar. Ze legt verder uit dat er een aantal aanpassingen nodig waren in het oorspronkelijke ontwerp om het project haalbaar te maken. “Het ontwerp was basaal uitgewerkt. Wij hebben als aannemer veel energie gestoken in het aanpassen en maakbaar maken van het ontwerp. Er waren problemen met de posities van kozijnen; details die gewoon niet bleken te kloppen,” legt ze uit. “Dit leidde tot noodzakelijke wijzigingen die ter plekke moesten worden doorgevoerd. Maar daar zijn we goed in bij K_Dekker.”
De keuze voor de locatie en de materialen die in het bouwproject zijn gebruikt, zoals de kleurrijke architectuur van het gebouw, maken het voor Tesselaar ook een bijzonder project. “Het gebouw heeft een ongebruikelijke koperen kleur, wat opvalt in de polder, maar het is een bewuste keuze van de architect geweest die goed uitpakt,” vertelt Tesselaar. Tegelijkertijd onthult Tesselaar enkele van de fysieke en planningsuitdagingen waarmee het team werd geconfronteerd, waaronder extreme weersomstandigheden die de bouwschema’s beïnvloedden. “We hebben extreem veel regen gehad, wat natuurlijk enorme impact heeft als je in een bouwbare fase zit waar de dakbedekking moet worden aangebracht.”
Flexibel
“Wat het ook een bijzonder project maakte, was dat er gebouwd is op het bouwterrein van een andere aannemer”, vertelt Hooijmans. “Die was daar tegelijkertijd bezig met het opstelterrein als onderdeel van de hele Uithoornlijn. Je kunt je voorstellen dat dit voor logistieke en plannings-uitdagingen zorgde. Gelukkig is K_Dekker een zeer flexibele aannemer die daar goed mee om kan gaan. Ze bewegen makkelijk mee bij onvoorziene omstandigheden. Voor ons werkt dat prettig.”
Beiden benadrukken het belang van samenwerking. “We kennen de weg bij GVB, weten hoe ze met veiligheid omgaan en wat ze van ons verlangen,” zegt Tesselaar. “Het scheelt dat we ook andere opdrachten voor ze uitvoeren. Dan ben je bekend met onderbrekingen zoals doorrijdende trams.”
PROJECTINFORMATIE
Nieuwbouw was- en zandvulgebouw GVB
Amstelveen
In de Legmeerpolder – tussen Amstelveen en Uithoorn – realiseert het GVB een nieuw rangeerterrein voor trams van de Amstelveenlijn die in 2024 doorgetrokken wordt naar Uithoorn en de Amstellijn gaat heten. K_Dekker bouwde het was- en zandvulgebouw op het terrein.
NIEUWSBRIEF
‘Nieuwe onderstations voor ProRail zijn prikkelend innovatief’
Gepubliceerd op 18 januari 2023
De overheid wil dat onze economie – bouw, bedrijven en organisaties – in 2030 voor vijftig procent circulair is. In 2050 moet dit honderd procent zijn. Deze ambities hebben een grote impact op ProRail en haar leveranciers zoals K_Dekker. Nieuwe technieken en aanpakken zorgen ervoor dat die transitie naar circulariteit slaagt. Dat is nog niet zo makkelijk in een van eisen en procedures omgeven werkveld. K_Dekker bouw & infra b.v. uit Warmenhuizen ontwerpt inmiddels dit modulaire- en biologisch vriendelijk onderstation. Een interessant pilot project.
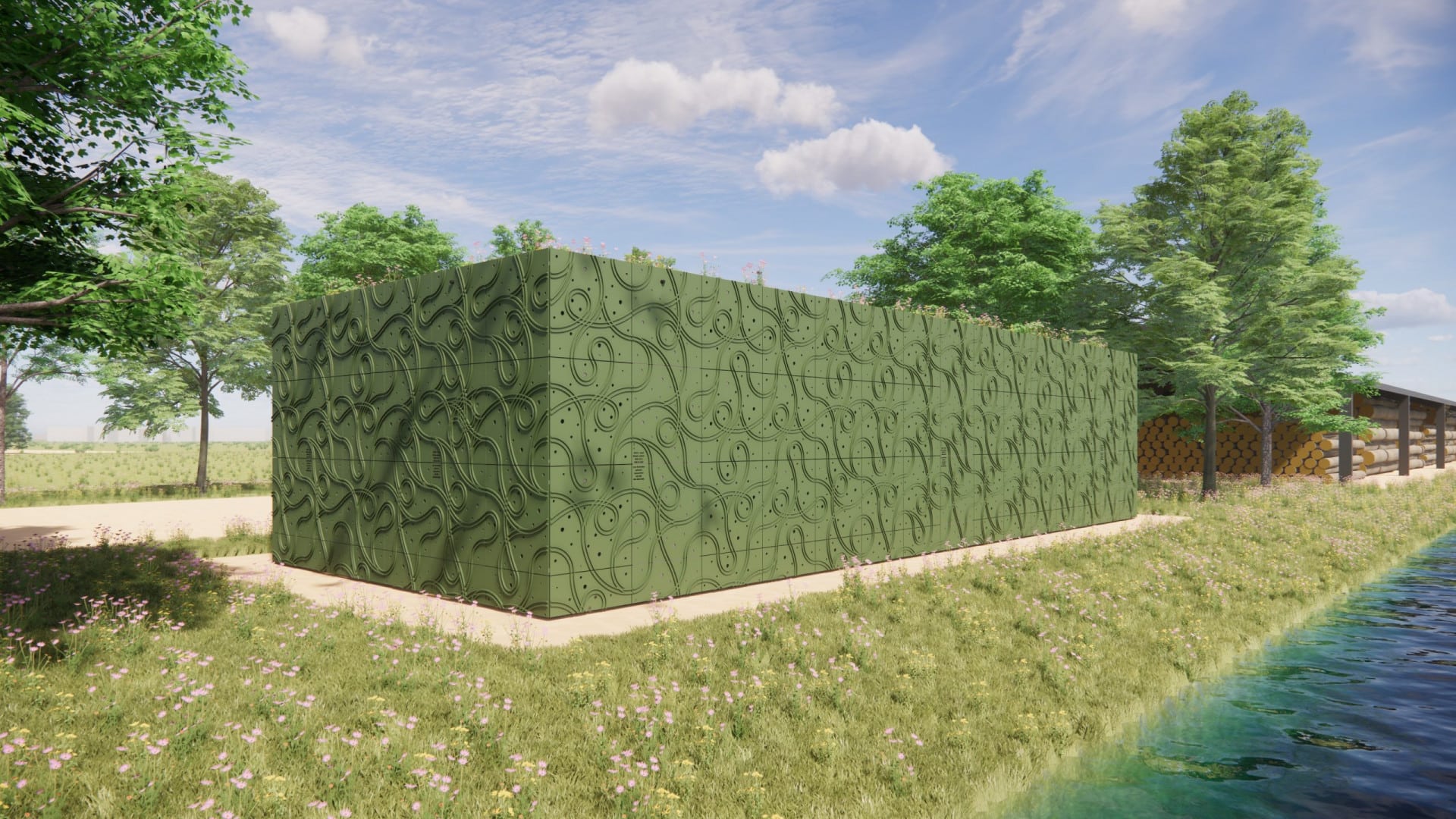
Een onderstation is een soort meterkast naast het spoor die de bovenleidingen voedt. Via een onderstation en kabels wordt de stroom geleverd waardoor treinen kunnen rijden. Zo’n onderstation kan qua afmetingen een balzaal zijn of een klein hokje. De grootte is afhankelijk van het aantal spoorbanen. Door de technologische ontwikkelingen is er minder ruimte nodig en kan het onderstation anders worden ingericht. De behuizing en het fundament van zo’n onderstation bestaat in de huidige setting uit beton, staal en stenen. Vooral grijs dus. Prorail wil de nieuwe onderstations circulair en modulair maken. Dit is prikkelend innovatief omdat de bouw hiervan veel regels kent.
Plug and play
Inmiddels loopt de pilot modulair onderstation al een tijdje. Prorail voert dit uit in gezamenlijkheid met K_Dekker. Ze zijn daar erg blij met deze innovatieve opdracht. Projectleider Frank Blom: ‘De onderstations staan vol elektrische voorzieningen (EV) en ICT, daar zou je ons als bouwkundig aannemer minder snel verwachten. Maar omdat het een circulair en modulair ontwerp betreft zijn we bij uitstek geschikt voor deze opdracht. De gedachte achter het modulaire onderstation is een soort ‘plug and play’.’
Modules
Je kunt het modulaire station – dat bestaat uit meerdere modules – samenstellen tot een functioneel onderstation en overal neerzetten. Ook bij calamiteiten kunnen de modules in zijn geheel snel uitgewisseld worden als dat nodig is. De basis van zo’n onderstation bestaat uit een fundatie van palen die boven het maaiveld uitsteekt. Daardoor ontstaat er een ruimte op het maaiveld waar de modules op staan. De modules zelf bestaan uit een houten vloer en wanden die zijn ingedeeld in compartimenten voor de transformatoren, kasten, ICT-toepassingen en dergelijke. Daaromheen wordt een architectonische buitenschil geplaatst bestaande uit bio-composiet panelen. Achter deze buitenschil bevindt zich een ruimte die wordt voorzien van nestkasten en bijenhotels. De buitenschil kan worden aangepast aan zijn omgeving.
Remonteren
“De bouwstoffen worden niet gebracht naar een bouwstoffen mortuarium, maar ze worden ge-remonteerd”, citeert Blom de duurzame architect Thomas Rau. Het modulaire en circulaire aspect van deze wijze van bouwen maakt het mogelijk om (delen van) het onderstation einde levensduur losmaakbaar te maken. Door die losmaakbaarheid kunnen onderdelen straks weer terug naar een bouwstoffen depot. Daar worden de bouwstoffen weer gehergroepeerd tot nieuwe bouwstoffen. Dit is nog geen praktijk, wel de sterke wens.
Intensieve samenwerking
Om het modulaire onderstation te realiseren werkt ProRail en K_Dekker met een heel team van verschillende specialisten van o.a. Movares. Dit is belangrijk voor het slagen van dit eerste ontwerp. De ontwerpvoorschriften (OVS-en), eisen en de modulaire en circulaire ideeën worden in bouwteams met elkaar besproken en vervolgens virtueel in 3D uitgewerkt. Zo is goed vast te stellen waar eventuele raakvlakken en vraagstukken zitten. Dat moet goed beschouwd en besproken worden, want enkele OVS-en liggen niet in lijn met het modulair en circulair bouwen van het station.
Gepuzzeld
ProRail en K_Dekker betrekken zoveel mogelijk relevante partijen bij het ontwerp. Dit voortraject en het virtueel bouwen verhoogt de kwaliteit en de uiteindelijke haalbaarheid van het modulaire onderstation. Als het ontwerp eenmaal klaar is, worden de modules gebouwd, ingericht en getest voordat ze naar de bouwplaats gaan. Wanneer alle vinkjes op groen staan worden ze naar de bouwplaats gebracht en -’plug en play’- geïnstalleerd. Als de pilot slaagt kunnen straks eventueel meerdere modulair onderstations in Nederland worden geplaatst. Maar zover is het nog niet. Eerst moet er nog gezamenlijk innovatief gepuzzeld worden om te komen tot een definitief goedgekeurd ontwerp.
Dit is een gastbijdrage van Nathalie Vrancken. Zij is werkzaam voor De Externe Voorzitter en is betrokken bij allerlei vormen van samenwerking, ook binnen de sector Bouw & Infra.
NIEUWSBRIEF
Werk aan de werf
Nieuwbouw ter uitbreiding gemeentewerf
Gepubliceerd op 1 juni 2022
Dat de gemeentewerf van Den Helder extra ruimte nodig had om de voertuigen droog en warm te kunnen stallen én dat de gemeente zelf een geschikte plek zocht voor de servers viel toevallig goed samen. K_Dekker bouwde een goed geïsoleerde loods aan de bestaande loods vast en realiseerde ook de inpandige MER-ruimte. “Geen complex werk, maar de tijd zat ons wel op de hielen.”
Voor de realisatie van de MER-ruimte – MER staat voor Main Equipment Room – en de loods moest er een onderheide betonvloer voorzien van stalen buispalen aangelegd worden, plus een stalen hoofddraagconstructie, dakisolatie, kalkzandstenen binnenwanden en buitengevelbekleding. Ook zorgde K_Dekker dat de E&W-voorzieningen van de ruimte werden geïnstalleerd, zodat de serverruimte daarna door de gemeente zelf ingericht, geinstalleerd en in gebruik genomen kon worden. In september 2021 startte K_Dekker met de werkzaamheden.
“En dat liep van begin af aan enorm gesmeerd. Eigenlijk zat alles mee: de materialen werden op tijd geleverd, de juiste mensen en machines waren op de juiste momenten beschikbaar en het was precies op de goede dagen droog weer”, vertelt Monique Lampe, projectleider namens K_Dekker. En dus werd de strakke deadline die de gemeente op het project had geplakt gewoon gehaald: in iets meer dan drie maanden was het hele project uitgedacht, ontworpen, berekend en uitgevoerd. “Binnen die termijn opleveren was een zeer belangrijke deadline: de gemeente wilde de servers op tijd installeren en operationeel hebben.”
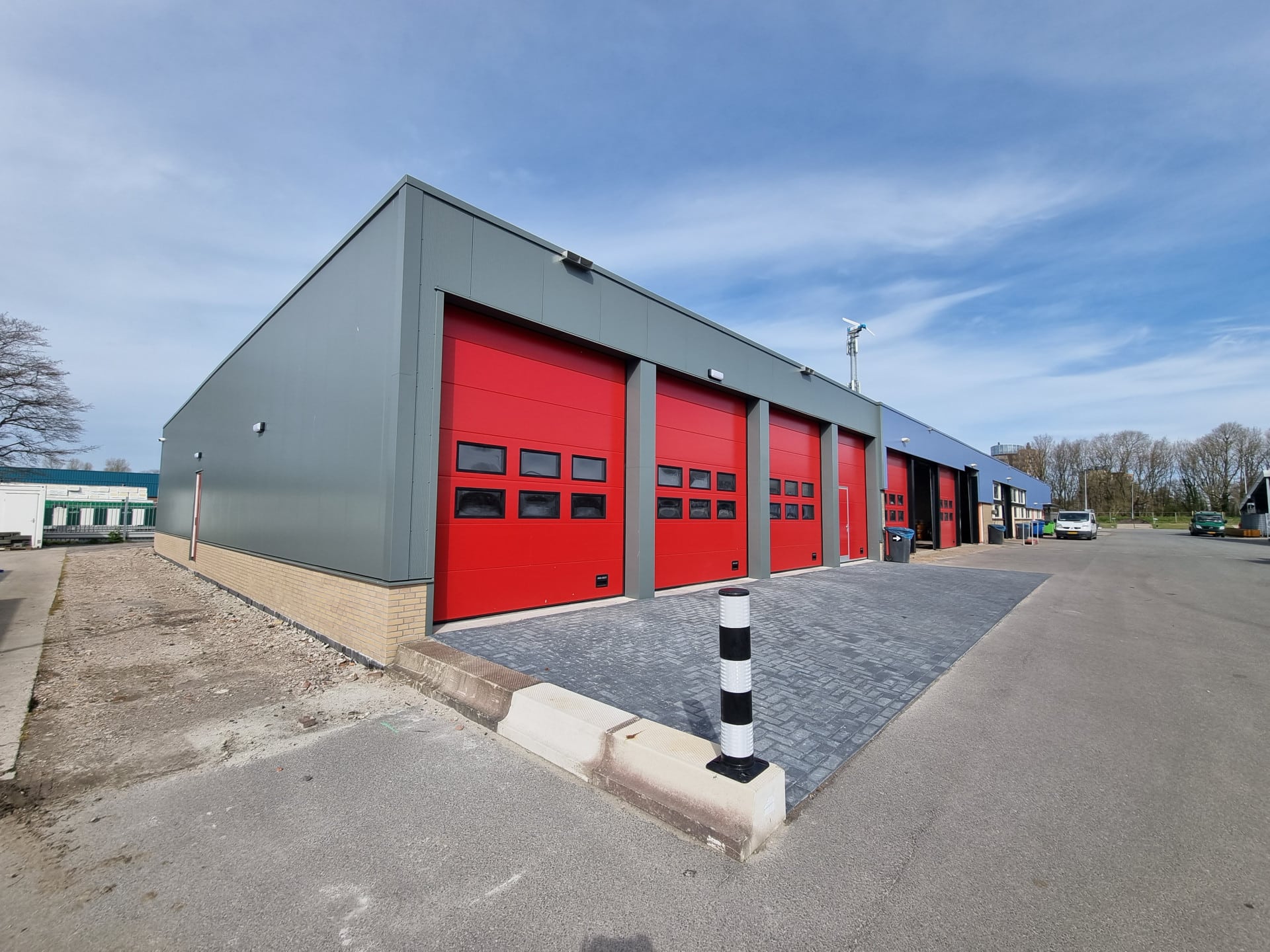
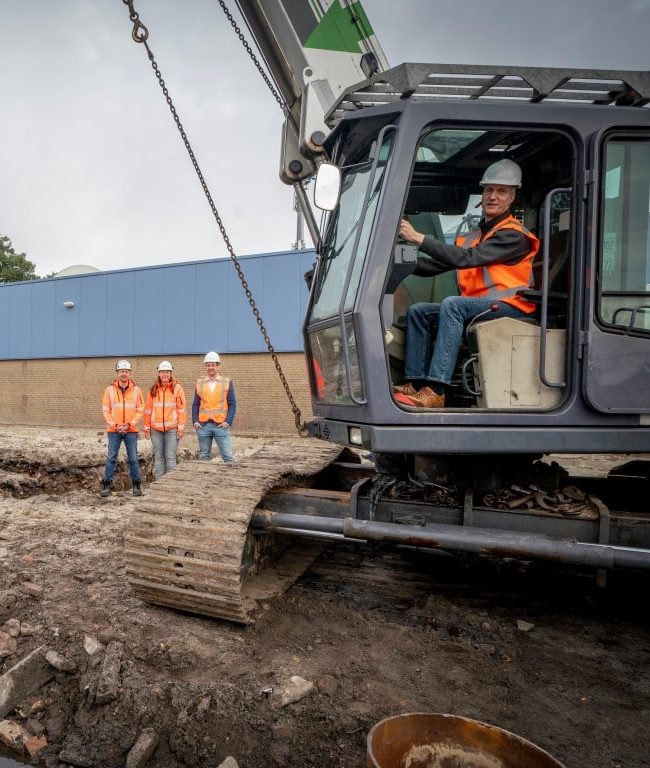
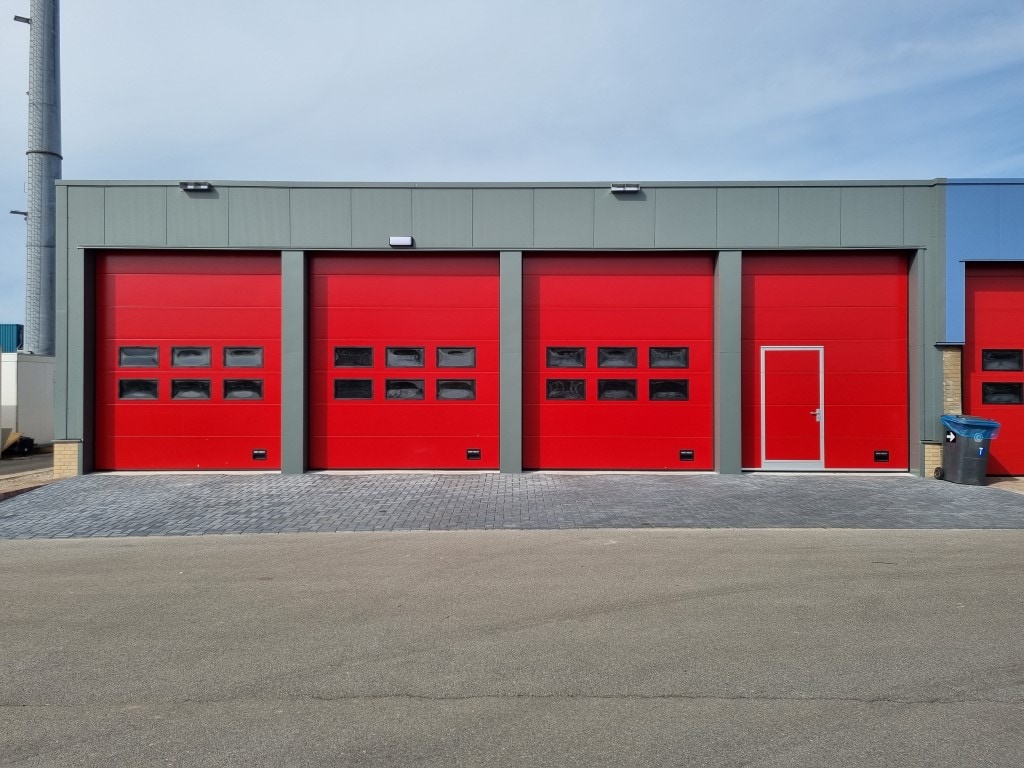
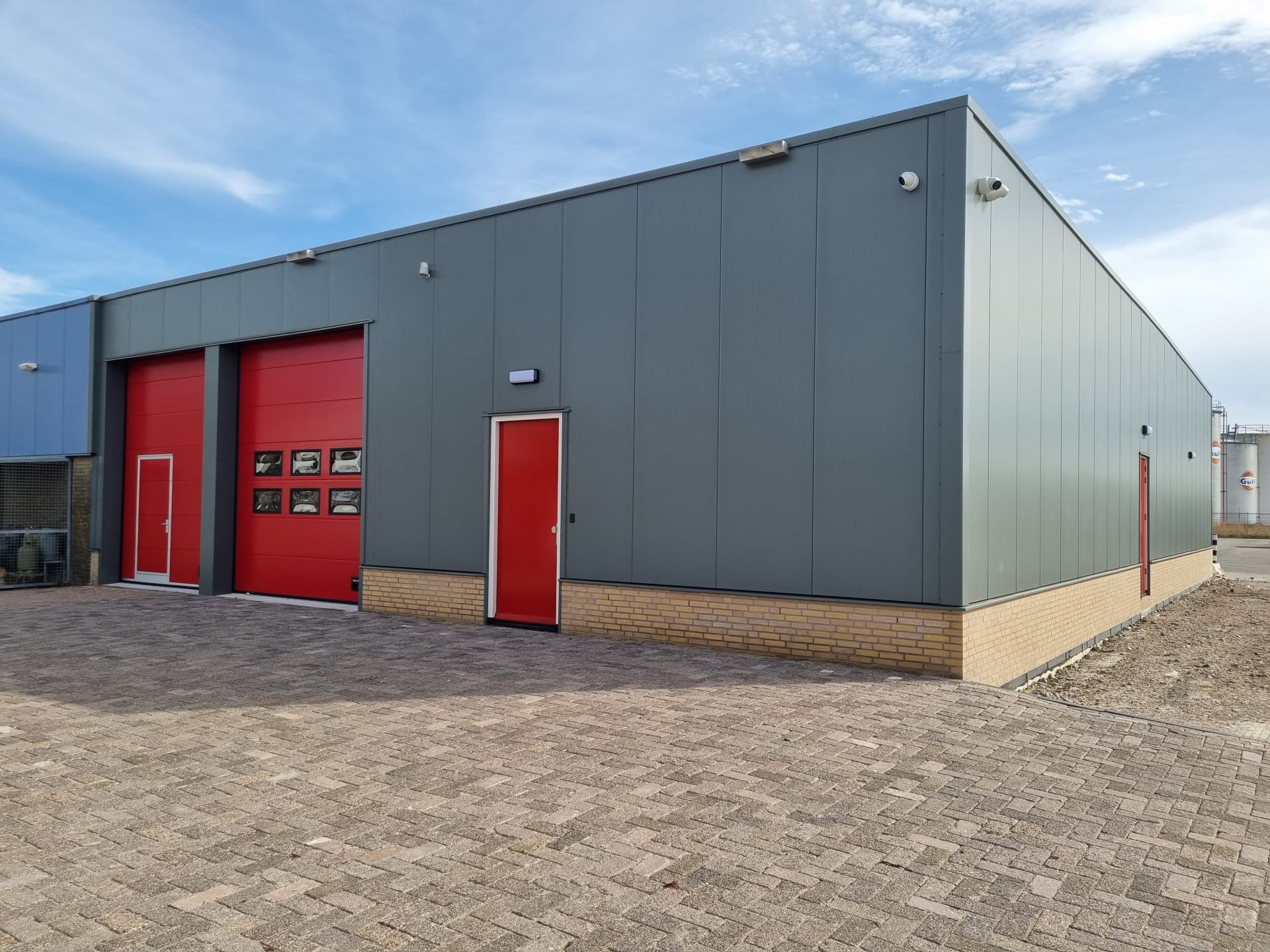
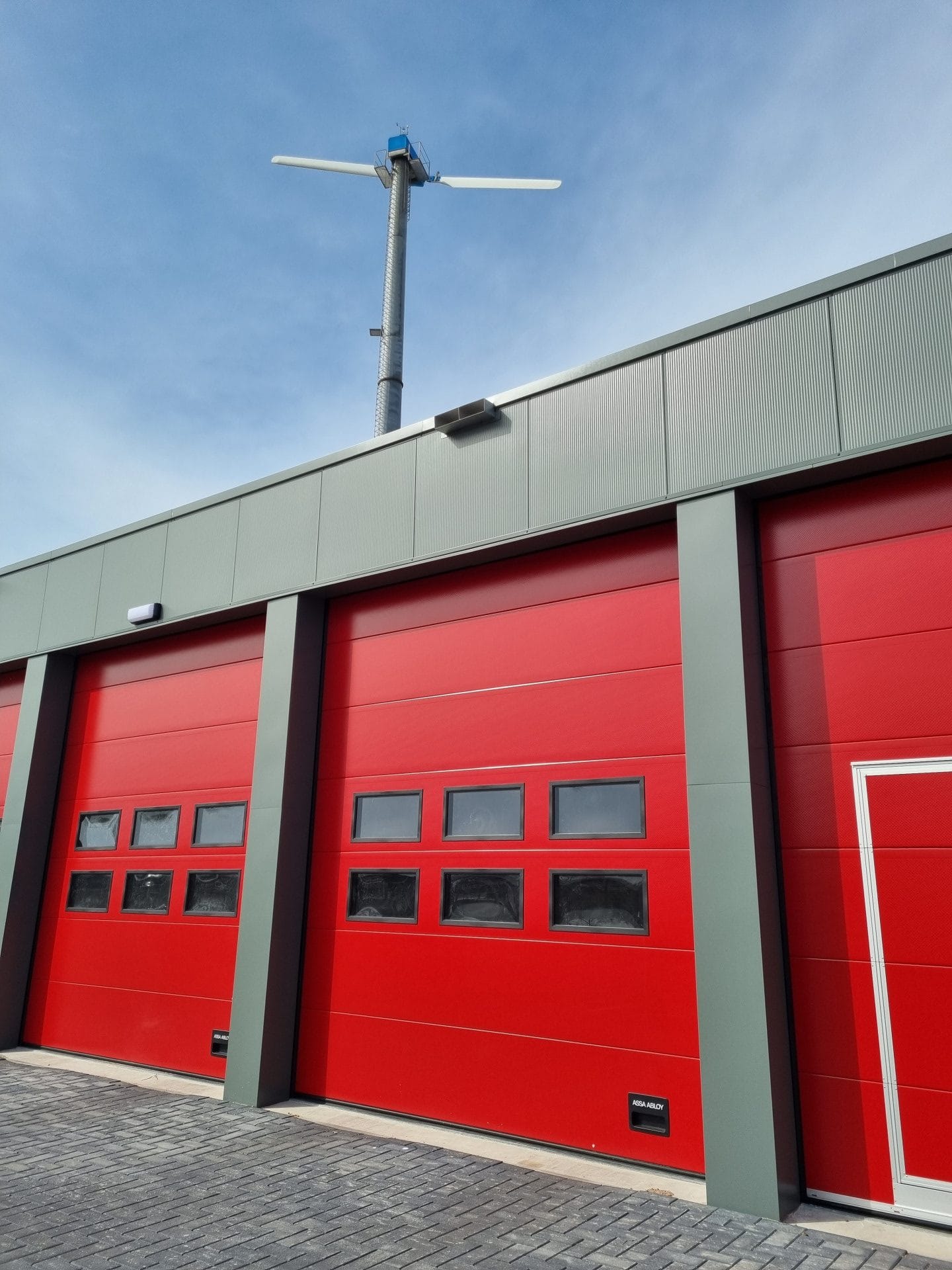
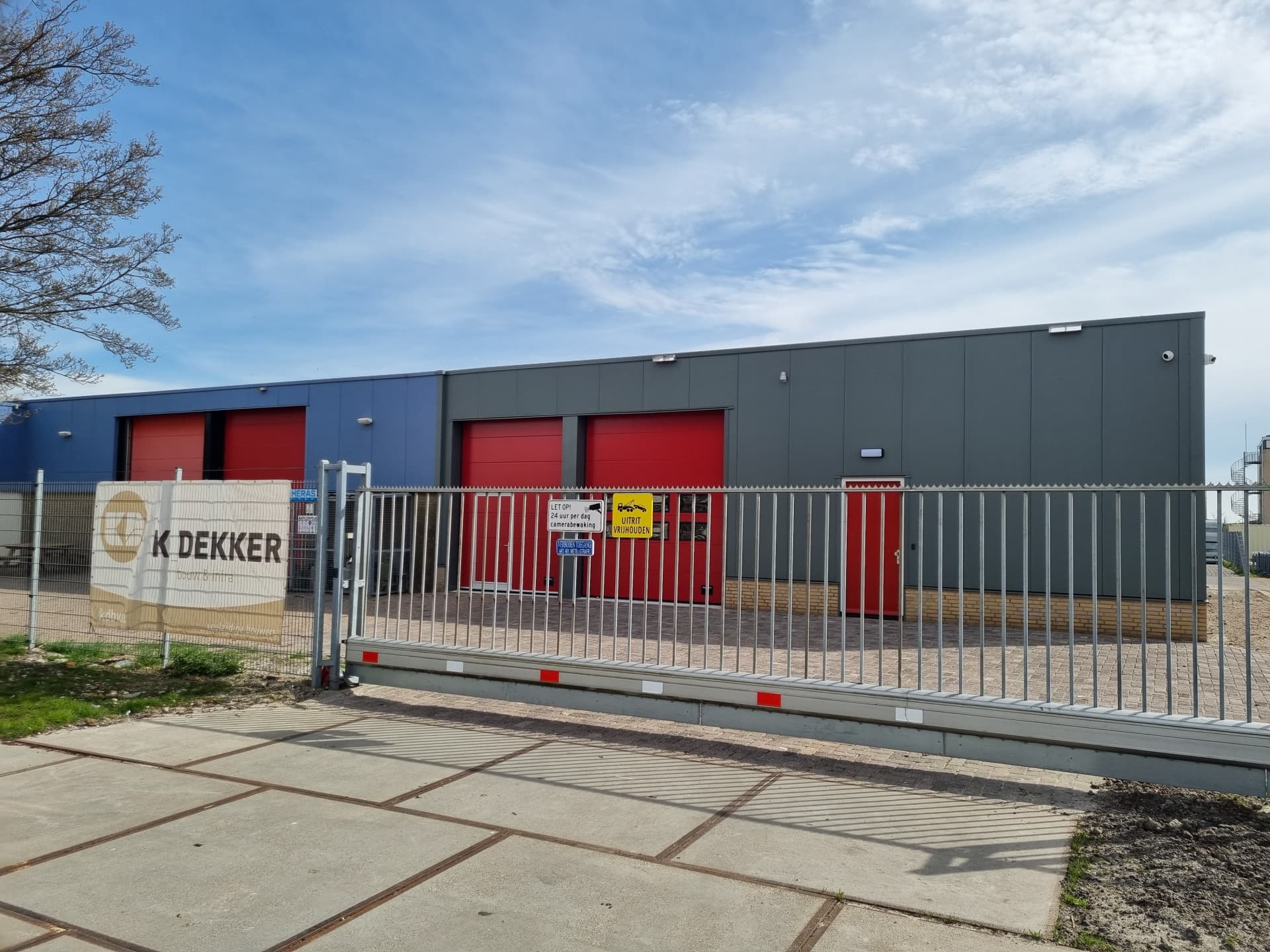
Risico’s afwegen
Met zoveel tijdsdruk was het team van K_Dekker extra scherp op mogelijke risico’s. “Die knelpunten hebben we ook minutieus doorgenomen met de opdrachtgever. We wilden geen van beiden voor verrassingen komen te staan. Maar toevallig viel het kwartje in dit project steeds de goede kant op”, zegt Monique Lampe. Dat kan Guido Meijer, de terrein- en wagenparkbeheerder van de gemeentewerf beamen. “Dankzij alle duidelijke afspraken liep de samenwerking bovendien uitstekend. Tijdens de verbouwing ging ons werk op de werf namelijk gewoon door. Toch stonden er op hooguit drie van de honderd dagen bijvoorbeeld auto’s in de weg. En dat werd met één belletje opgelost.”
Dat K_Dekker het ontwerp van de loods en de MER-ruimte grotendeels zelf had uitgewerkt bleek een belangrijk voordeel bij een aantal kleine maar cruciale bouwkundige aanpassingen. “Doordat we het plan perfect kenden, konden we ook snel schakelen als dingen net even anders moesten. Dit werk was technisch gezien misschien niet zo complex, qua afstemming en flexibiliteit zaten we wel op het hoogste level”, vertelt Monique Lampe.
PROJECTINFORMATIE
Nieuwbouw ter uitbreiding gemeentewerf
Den Helder
Nog voor 2022 wil de gemeente Den Helder een nieuwe dataserver operationeel hebben. Daarvoor moet een Main Equipment Room – een MER-ruimte – opgetuigd worden op de gemeentewerf. K_Dekker breidt daarvoor de bestaande loodsen op de werf uit met een compleet nieuw gebouw.
NIEUWSBRIEF
Restproduct, en vól energie!
Biomassa-installatie bij Olam Food Ingredients
Gepubliceerd op 1 juni 2022
De cacaofabriek van Olam Food Ingredients in Koog aan de Zaan reduceert straks vijftig procent van het gasverbruik door in een biomassa-installatie de eigen cacaodoppen te verbranden. “Goed voor het milieu én goed voor ons bedrijf.” K_Dekker realiseerde het gebouw voor de biomassa-installatie.
Wat voor de onwetende buitenstaander alleen een fors en tamelijk rechttoe-rechtaan pand lijkt, vergde toch heel wat denk- en rekenwerk. Ook moest het team van K_Dekker flink tempo maken – de planning was strak opgezet. “Omdat de installatie al vrijwel volledig stond was het zaak om het geheel zo snel mogelijk wind- en waterdicht te krijgen”, vertelt projectcoördinator Kevin van der Veekens. Flexibel en snel kunnen schakelen zijn dan geen overbodige luxe.
Staalconstructie
De biomassa-installatie staat op het fabrieksterrein van Olam. K_Dekker had eerder de projectlocatie al bouwrijp gemaakt en de terreinverharding aangebracht. Een derde partij had vervolgens de betonvloer gestort. Daarna bestond het werk voor K_Dekker uit het neerzetten van de enorme stalen constructie van 25 meter hoog en het aanbrengen van isolatiemateriaal en gevelbekleding. “Een van de lastigheden waar we tegenaan liepen was de krappe bouwplaats. Direct aan de achterkant liep een sloot. Daarvoor hebben we plateaus in het water gelegd zodat we er met ons materieel bij konden komen. De achtergevel hebben we later vanuit hangbakken gemonteerd, en de regenafvoer via rope access: abseilend als het ware”, legt Kevin van der Veekens uit. Never a dull moment, daar in Koog aan de Zaan.
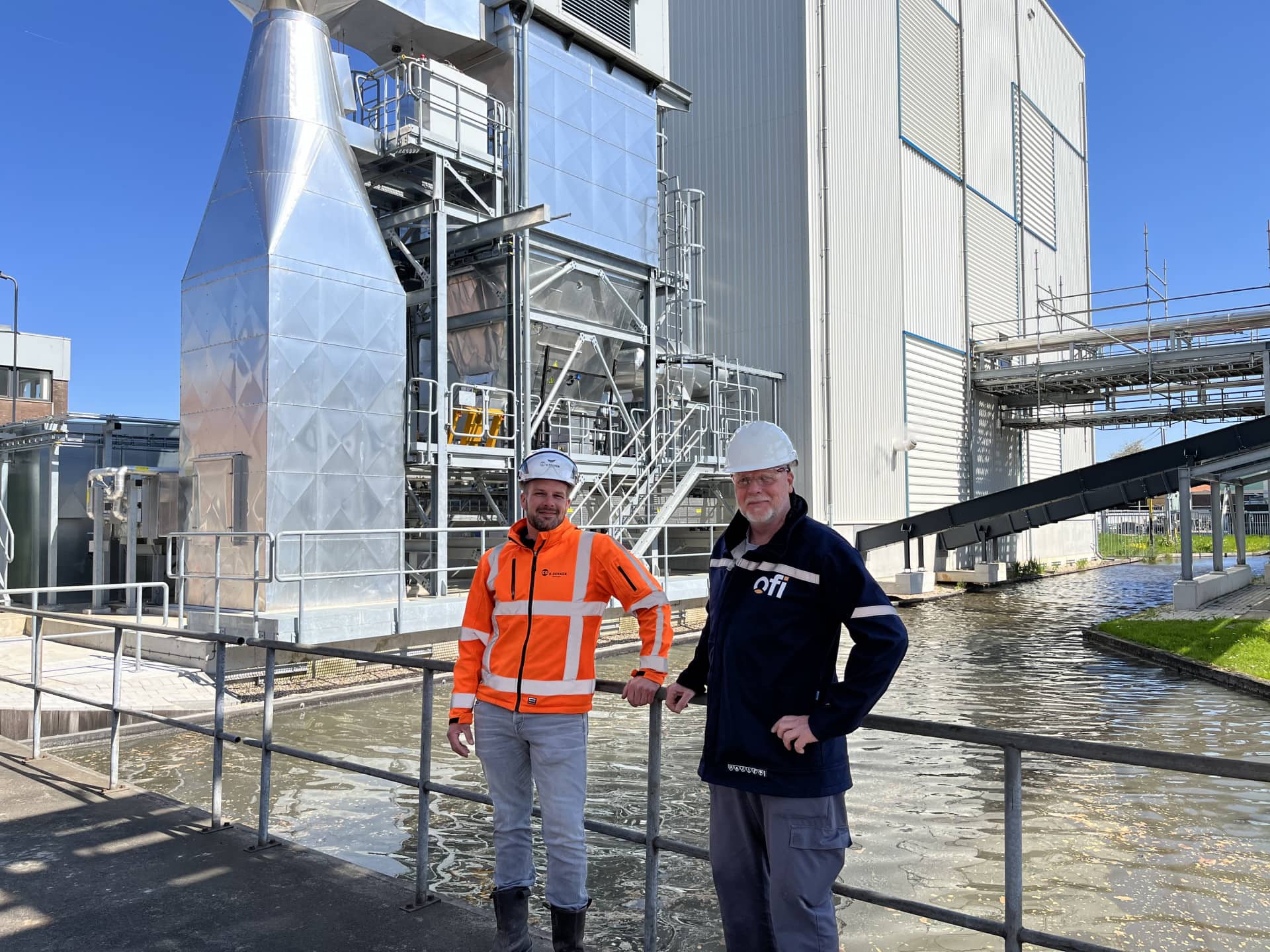
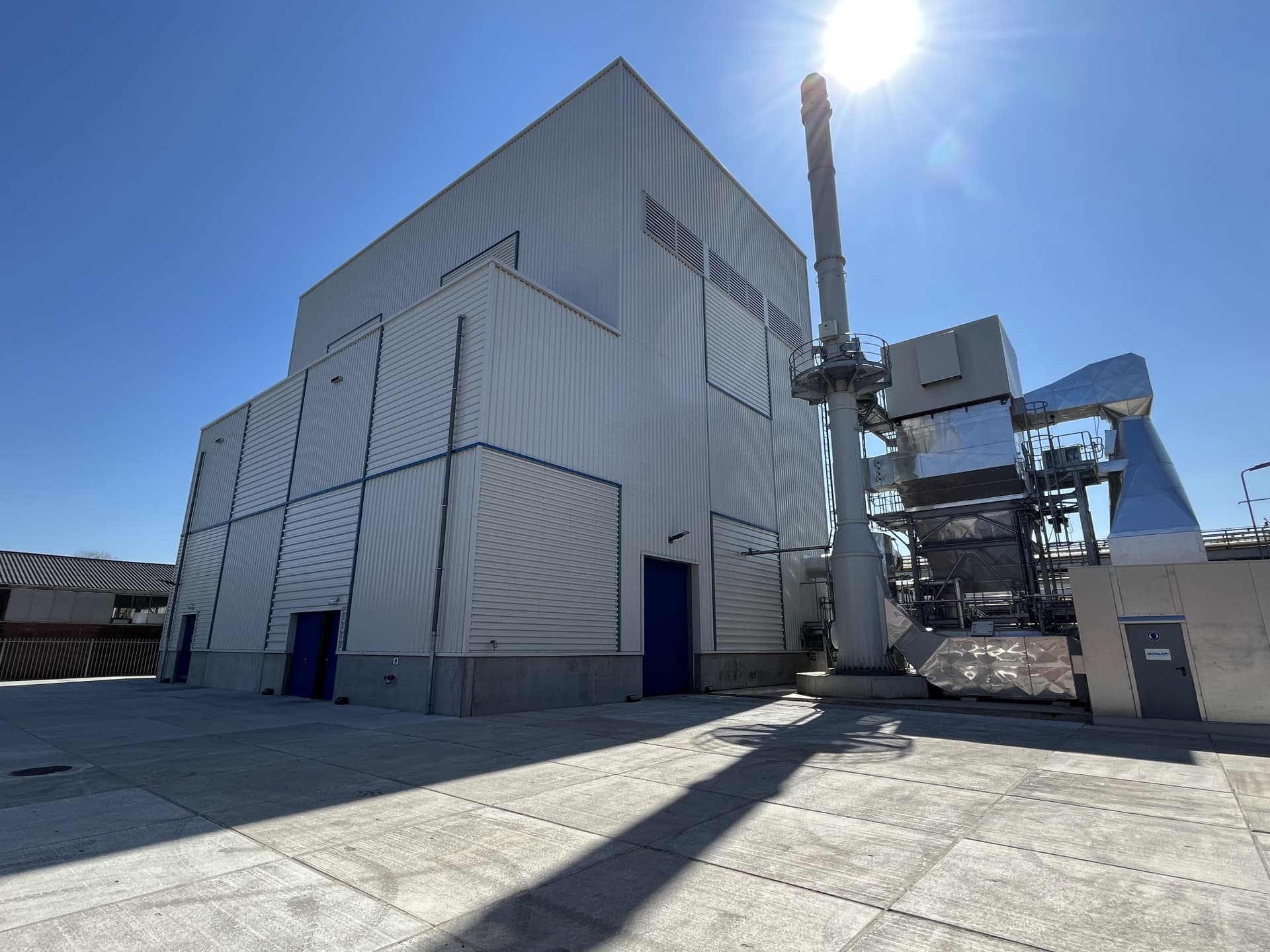
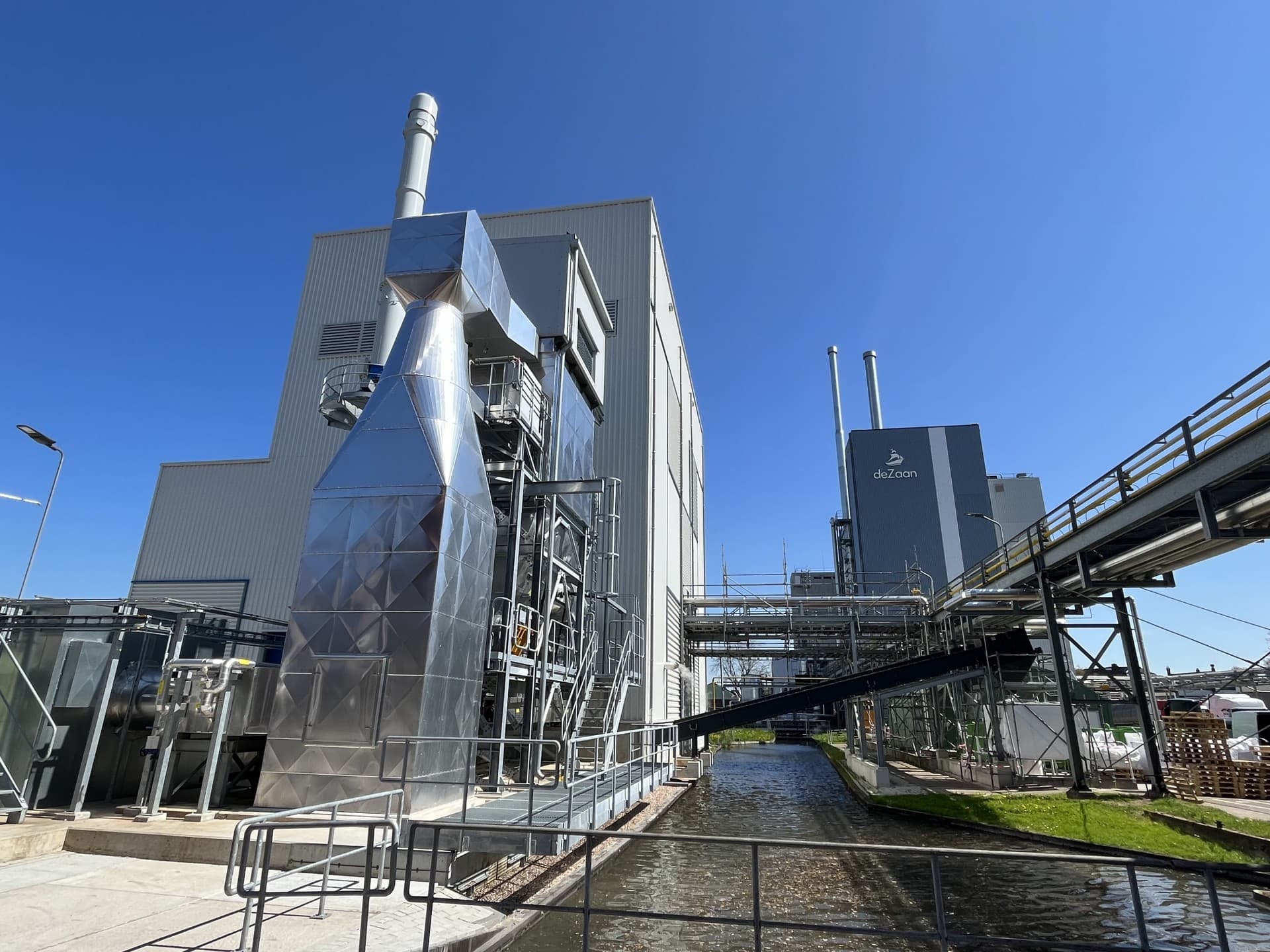
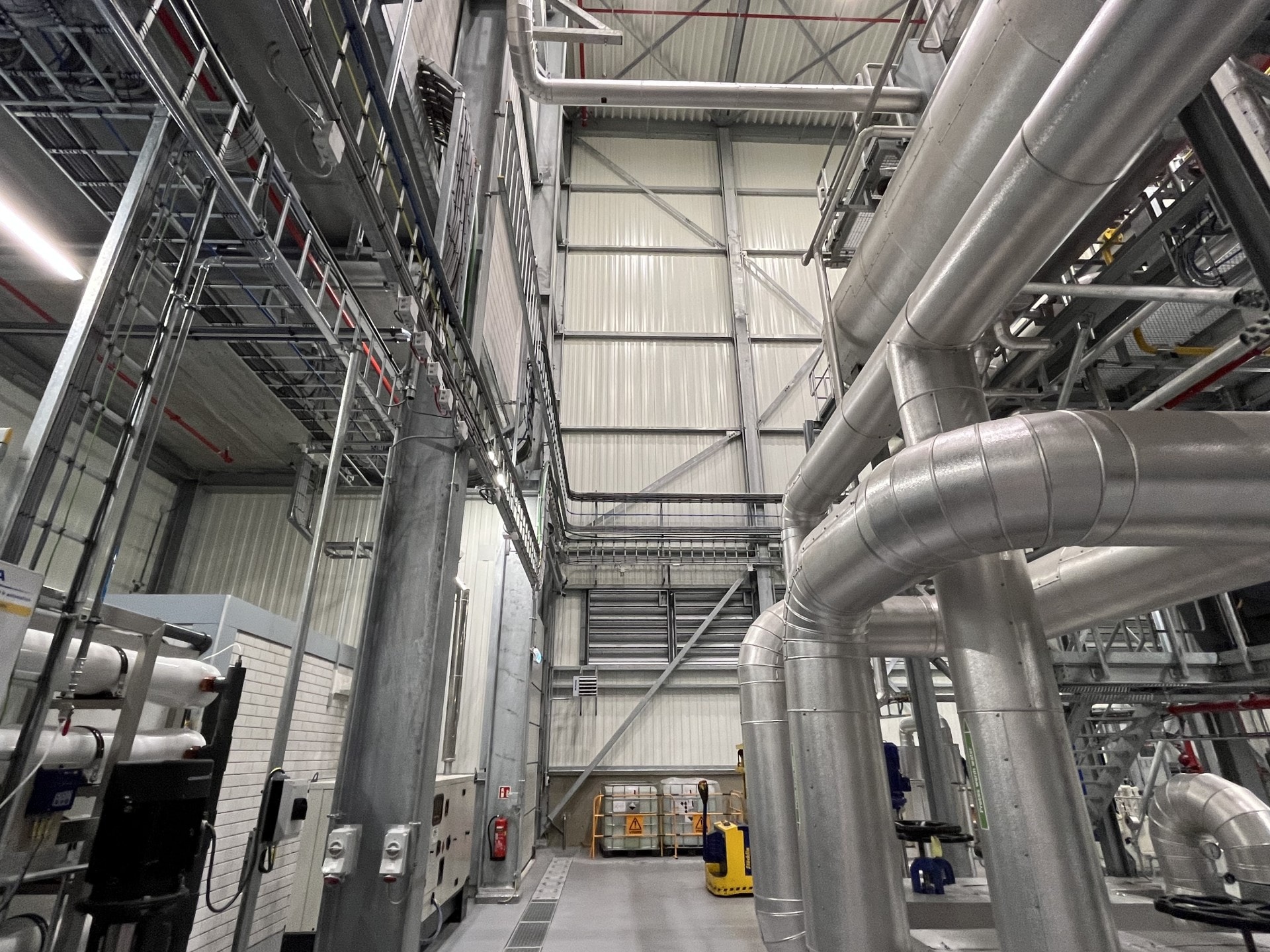
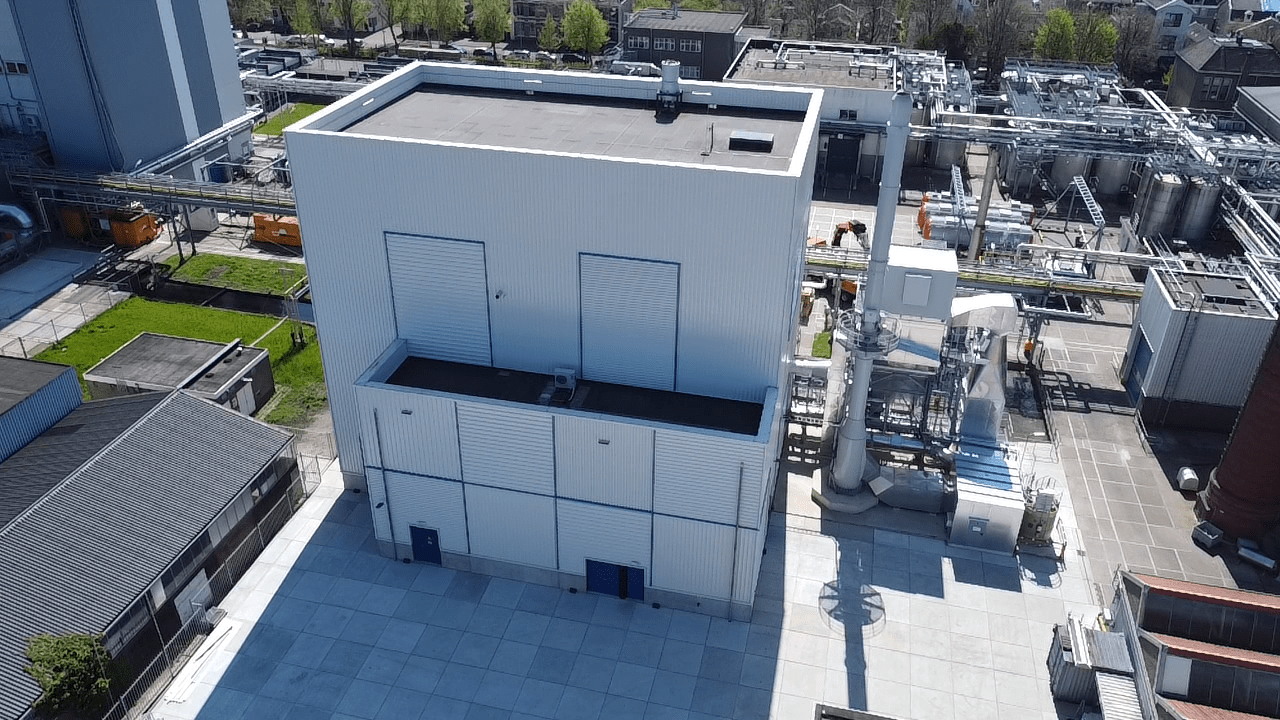
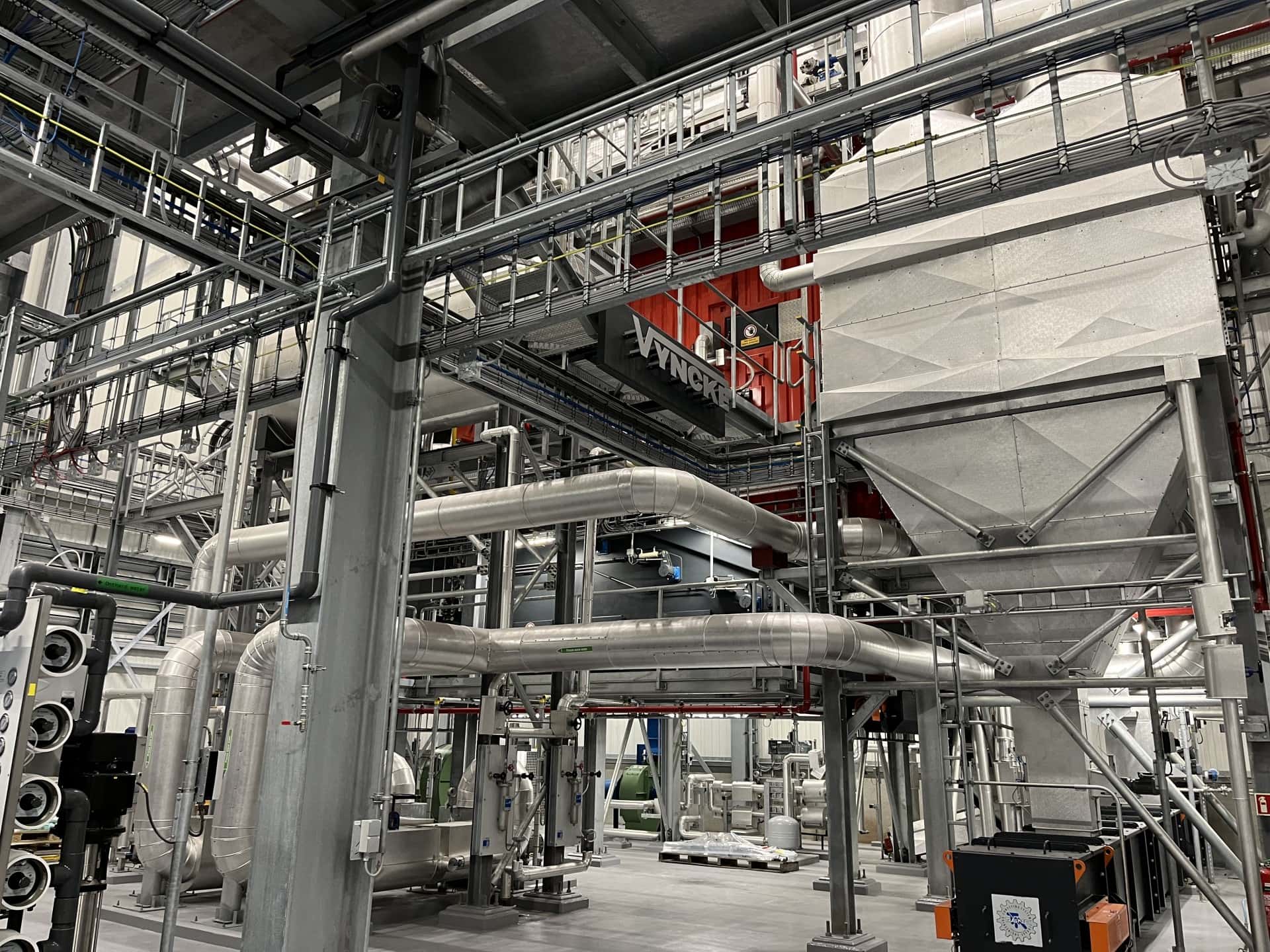
Safety first
“Bij K_Dekker weten we wat veilig werken is. Niet voor niets zitten we inmiddels op trede 4 van de Veiligheidsladder. Toch waren we bij Olam extra alert. Onder meer omdat er in de fabriek gewoon werd doorgewerkt tijdens het bouwproject, de bouwruimte krap was en er ook andere partijen actief waren”, vertelt Kevin van der Veekens. Dat het qua veiligheid in het bijzonder en qua samenwerking in het algemeen goed verliep, kan technisch manager René Sturm alleen maar beamen. “Het team van K_Dekker dacht steeds constructief mee bij onverwachte tegenvallers. Ze stonden open voor andere oplossingen, de deadline verloren ze niet uit het oog. Echt teamwork dus.”
Dubbel profijt
De biomassa-installatie bij Olam Food Ingredients in Koog aan de Zaan moet straks het gasverbruik van de fabriek met vijftig procent terugdringen. Gunstig in economisch en milieutechnisch opzicht. René Sturm: “We verbruiken straks de helft minder gas. Daarnaast dringen we ook het aantal transportbewegingen fors terug. Tot nu toe werden onze cacao-doppen afgevoerd als afval – al die kilometers vallen weg. Natuurlijk is het ook in bedrijfseconomische zin goed: we worden minder afhankelijk en besparen op energiekosten met onze eigen energiecentrale.”
PROJECTINFORMATIE
Biomassa-installatie bij Olam Food Ingredients
Koog aan de Zaan
Op het terrein van de cacaofabriek van Olam Food Ingredients in Koog aan de Zaan realiseerde K_Dekker het gebouw voor een biomassa-installatie waarin cacaodoppen verbrand worden.
NIEUWSBRIEF
Gemeentewerf Ambachtsweg wordt verduurzaamd
Nieuwbouw ter uitbreiding gemeentewerf
Gepubliceerd op 4 oktober 2021
Het gemeentegebouw aan de Ambachtsweg in Den Helder wordt de komende maanden uitgebreid en verduurzaamd tot een ‘nul-op-de-meter’-gebouw. Met isolatie, dubbelglas, een lucht-warmtepompinstallatie en met een slim, modern gebouwbeheersysteem wordt er jaarlijks niet meer energie gebruikt, dan dat de 440 zonnepanelen op het dak zullen gaan opleveren. Afgelopen vrijdag 1 oktober sloeg wethouder Remco Duijnker de eerste paal in de grond voor de uitbreiding van het pand.
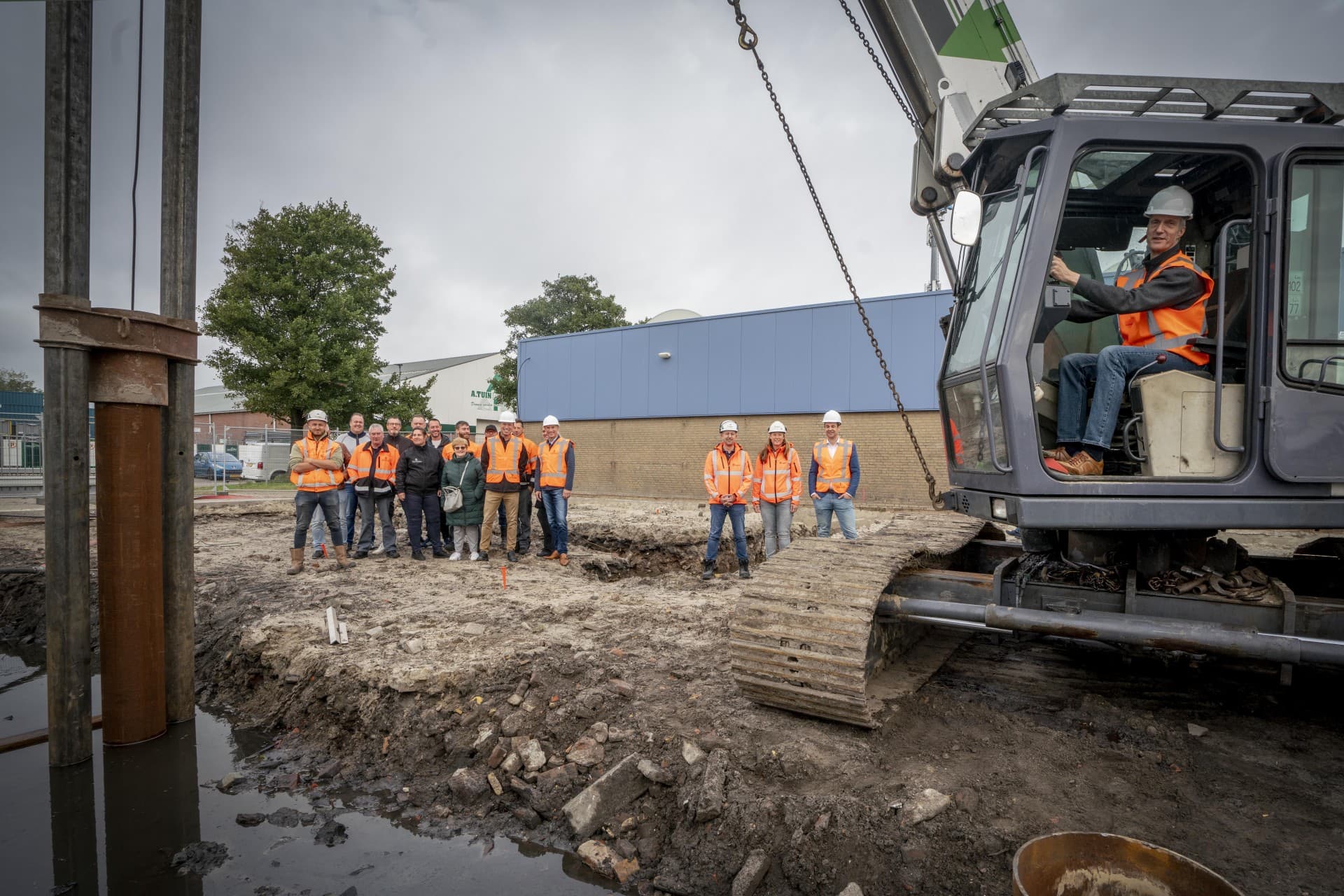
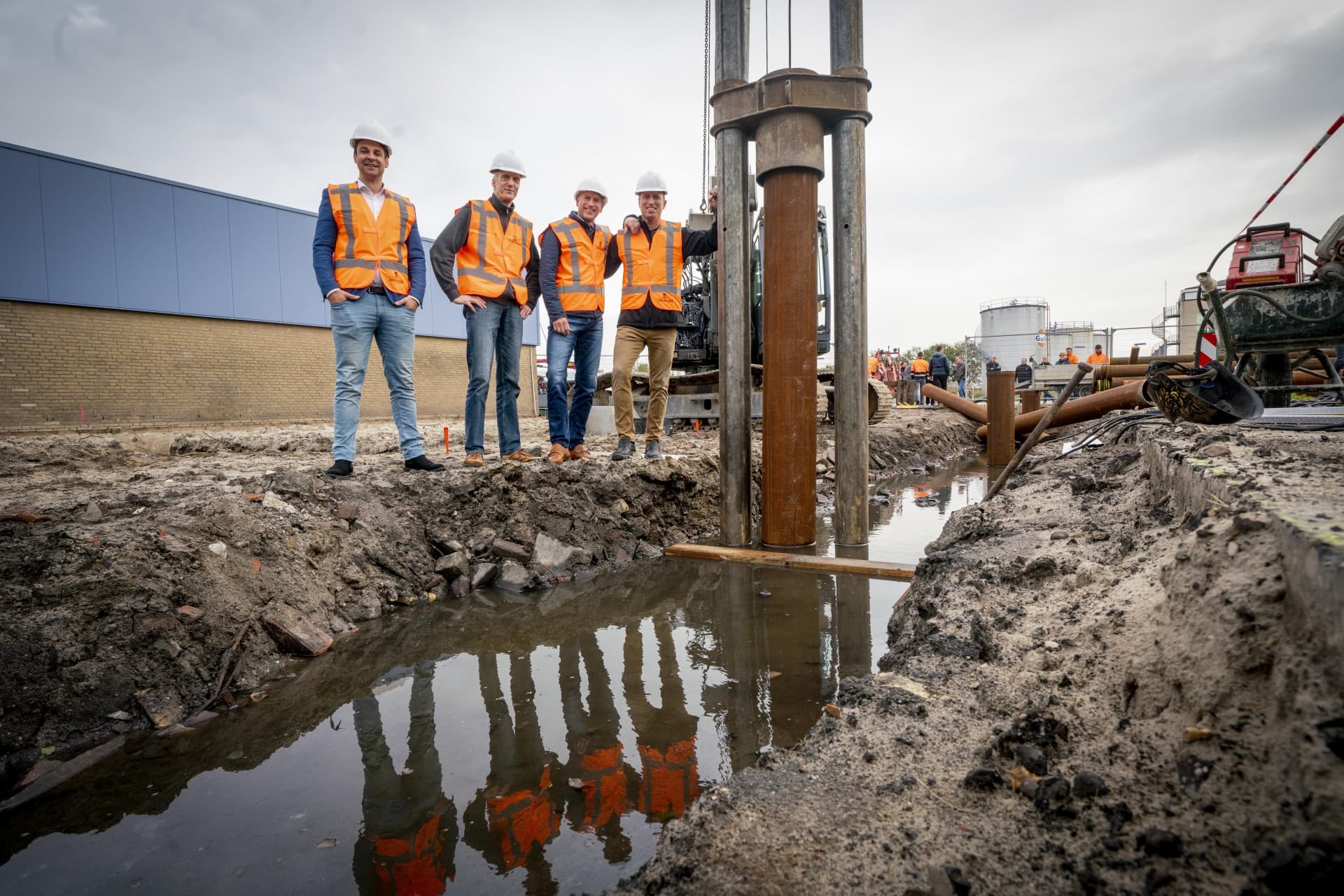
Het gebouw aan de Ambachtsweg is de thuishaven van team Wijkbeheer, dat al het gemeentelijk onderhoud in Den Helder uitvoert. Het huidige gebouw aan de Ambachtsweg blijft grotendeels staan. Aannemer K. Dekker uit Warmenhuizen tekende voor de opdracht. Verwacht wordt dat de modernisering en de uitbouw volgend jaar klaar zijn. De aannemer brengt spouw- en dakisolatie aan en er komt dubbelglas. Op het dak komen 440 zonnepanelen, met een verwachte opbrengst van 110.000 kWh/jaar. Dat komt overeen met het verwachte toekomstige verbruik.
De uitbouw van het pand is nodig voor het huisvesten van MER-ruimte. MER staat voor Main Equipment Room. Deze ruimte is nu nog gehuisvest in het pand aan de Bijlweg. Hierin staan de servers van de gemeente en het is daarmee het netwerk-hart van de gemeentelijke organisatie. Een ander deel van de uitbouw aan de Ambachtsweg is bestemd voor de opslag van grootmaterieel. Door wagens en machines onderdak te geven, kunnen ze langer meegaan. In de toekomst zal de gemeente nog meer gebouwen gaan verduurzamen: “Als gemeente willen we het goede voorbeeld geven om duurzame maatregelen te treffen in en rondom onze gebouwen. Zoals met de ingebruikname van de tankinstallatie voor blauwe diesel. En nu voor het slaan van de eerste paal van de energiezuinige uitbouw van de Ambachtsweg. Dit jaar verduurzamen we ook nog vier gemeentelijke gymzalen, onder andere door nieuwe isolatie en dubbel glas. Daarmee besparen we energie en kosten”, aldus de wethouder.
BRON: Regio Noordkop
PROJECTINFORMATIE
Nieuwbouw ter uitbreiding gemeentewerf
Den Helder
Nog voor 2022 wil de gemeente Den Helder een nieuwe dataserver operationeel hebben. Daarvoor moet een Main Equipment Room – een MER-ruimte – opgetuigd worden op de gemeentewerf. K_Dekker breidt daarvoor de bestaande loodsen op de werf uit met een compleet nieuw gebouw.
NIEUWSBRIEF
Renovatie Dunea Katwijk
Katwijk
Gepubliceerd op 24 september 2021
Een bijzonder en uniek project waar wij in opdracht van Dunea aan werken is de realisatie van een nieuwe spoelwaterverwerkingsinstallatie en de restauratie van het monumentale Voorfiltergebouw in Katwijk. De restauratie van het Voorfiltergebouw en de bouwkundige werkzaamheden van de nieuwe installatie zijn inmiddels gereed. De nieuwe installatie is middels een zogeheten doos-in-doos constructie verwerkt in het monumentale voorfiltergebouw, dit maakt dat het prachtige authentieke aanzicht behouden blijft.
Momenteel zijn we bezig met de volgende fase, waarin de installatiewerkzaamheden worden uitgevoerd en zijn gestart met de civiele werkzaamheden: het aanleggen van putten, terreinleidingen, -verhardingen, de aanpassing van twee bestaande bufferbezinkers en het dempen van de infiltratieplas. Aansluitend wordt ook een bergingsbuffer, een verbeterde slibopslag en een wasvoorziening voor transportmaterieel gerealiseerd.
In samenwerking met: Logisticon Water Treatment | Elmon Elektro installatie / Besturingstechniek | Installatiebureau Rutgers | C.A. de Groot Groep BV | Pronk Bouw | MEESTERS IN
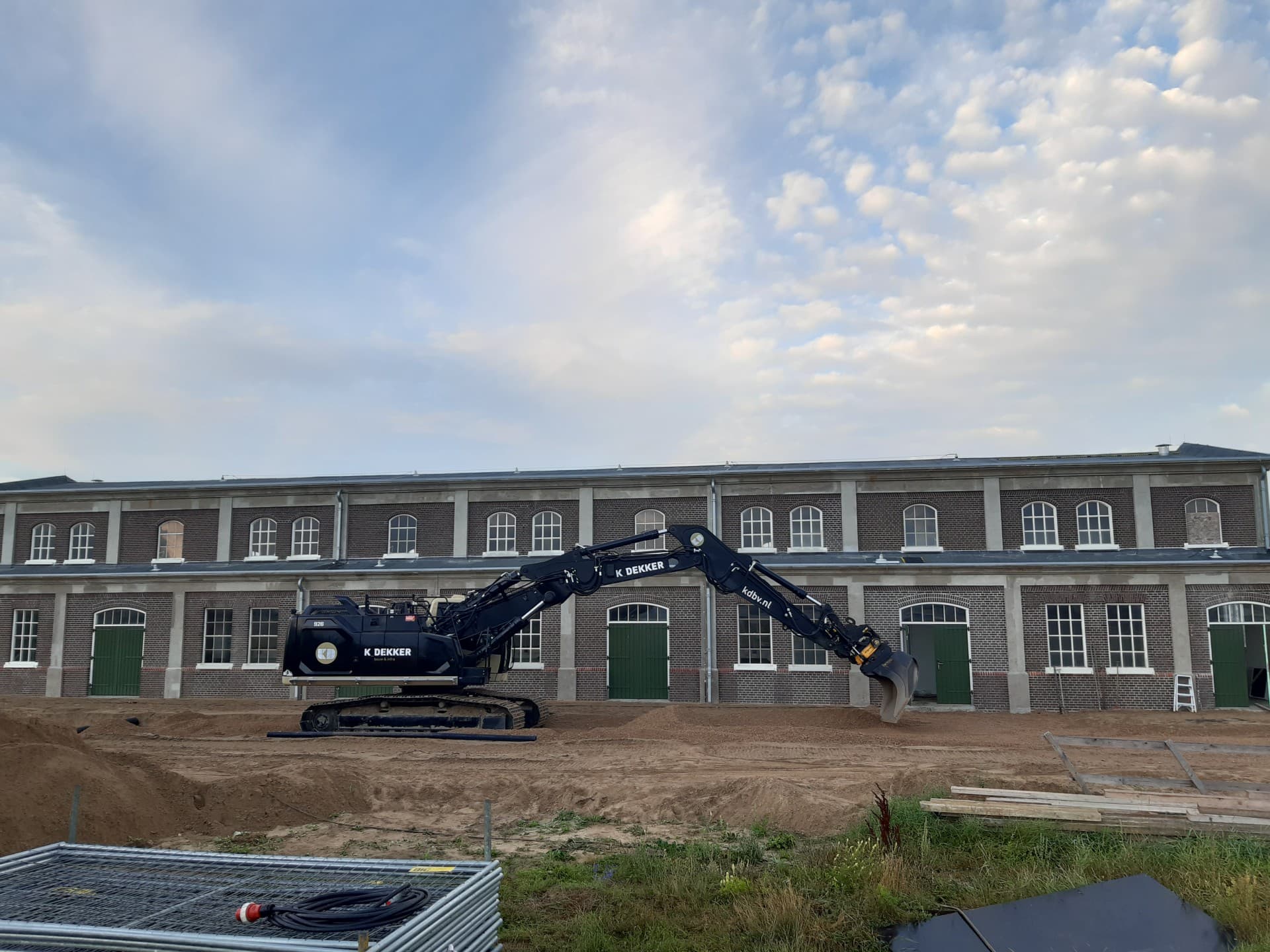
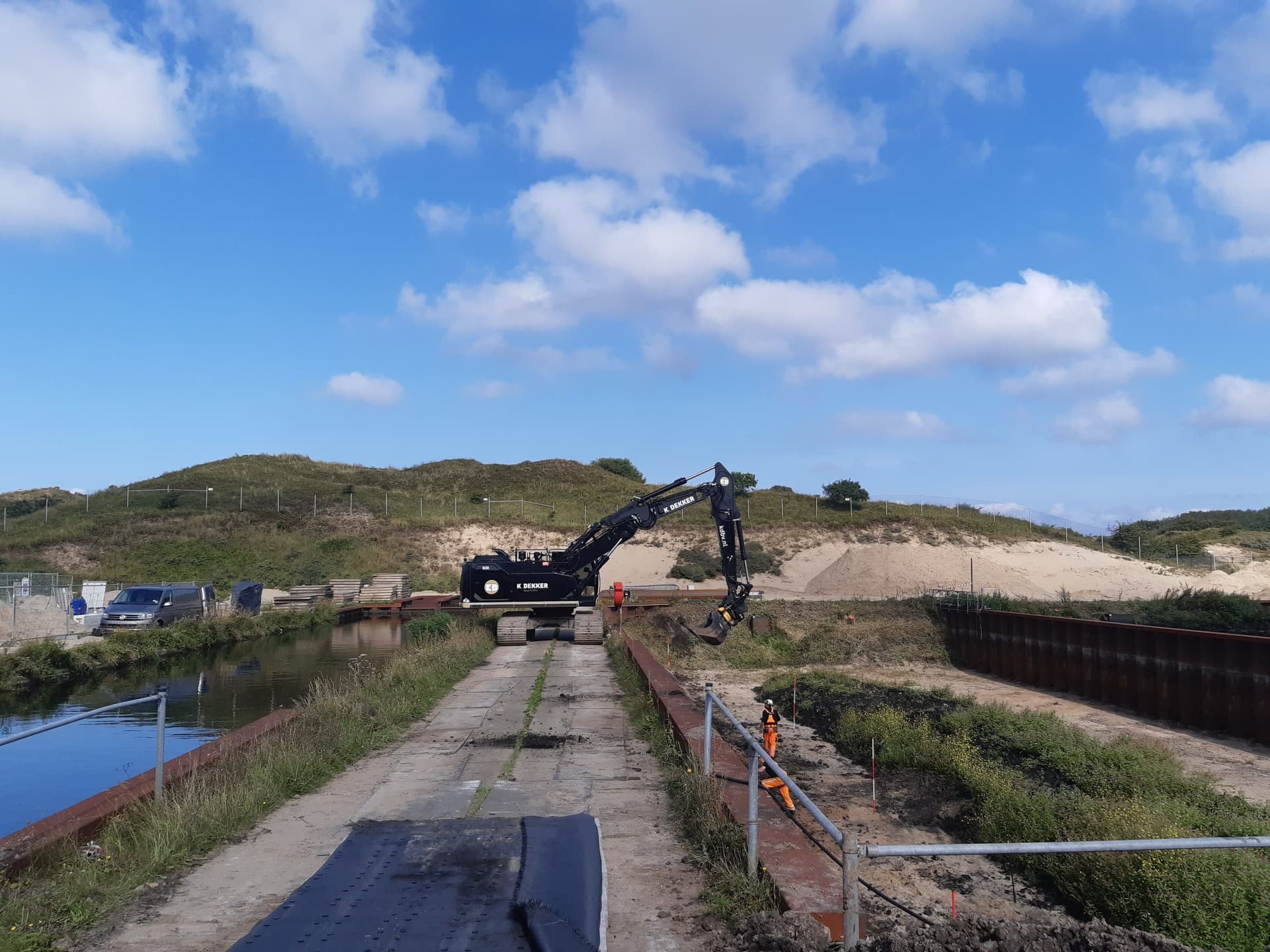
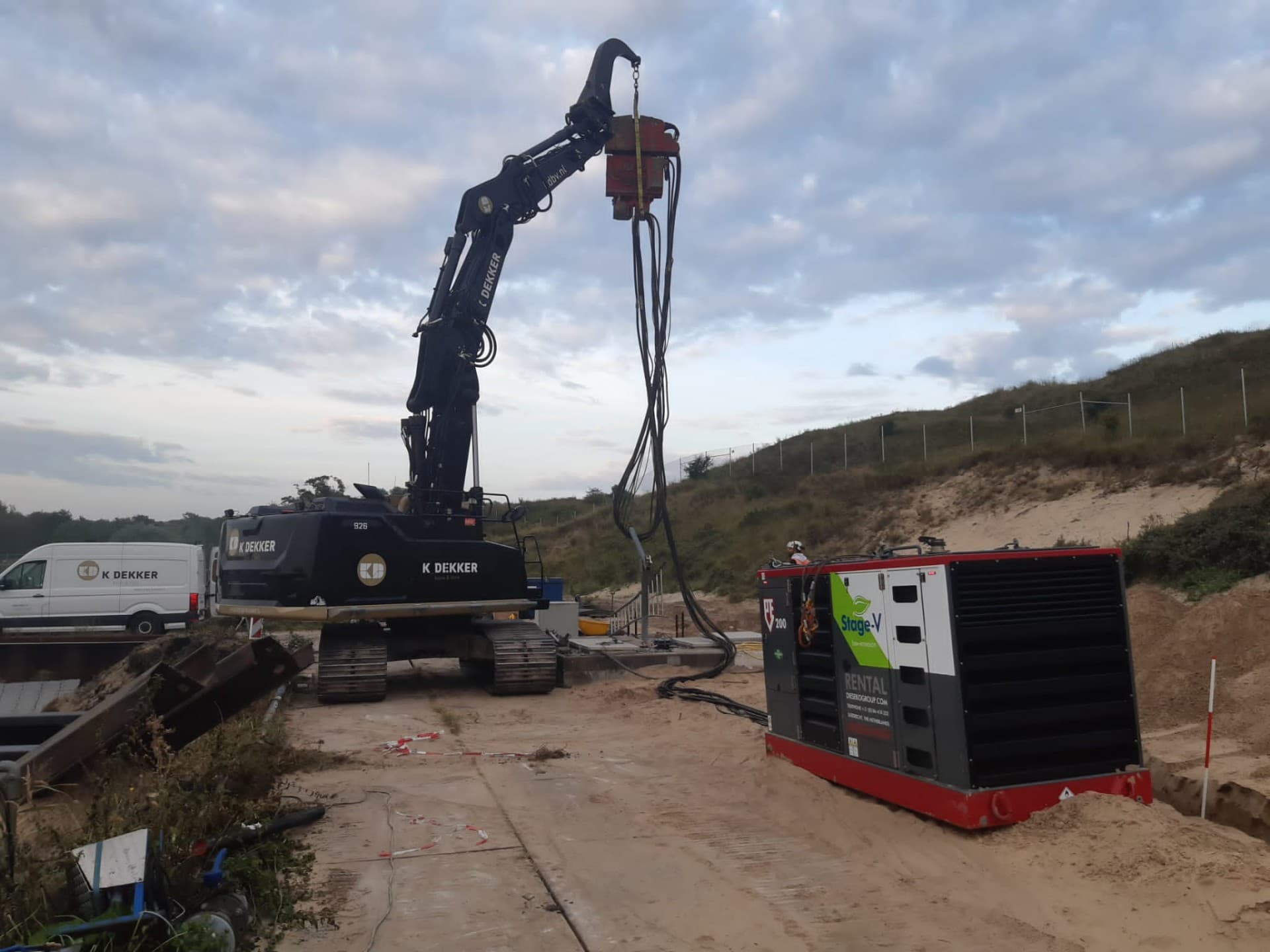
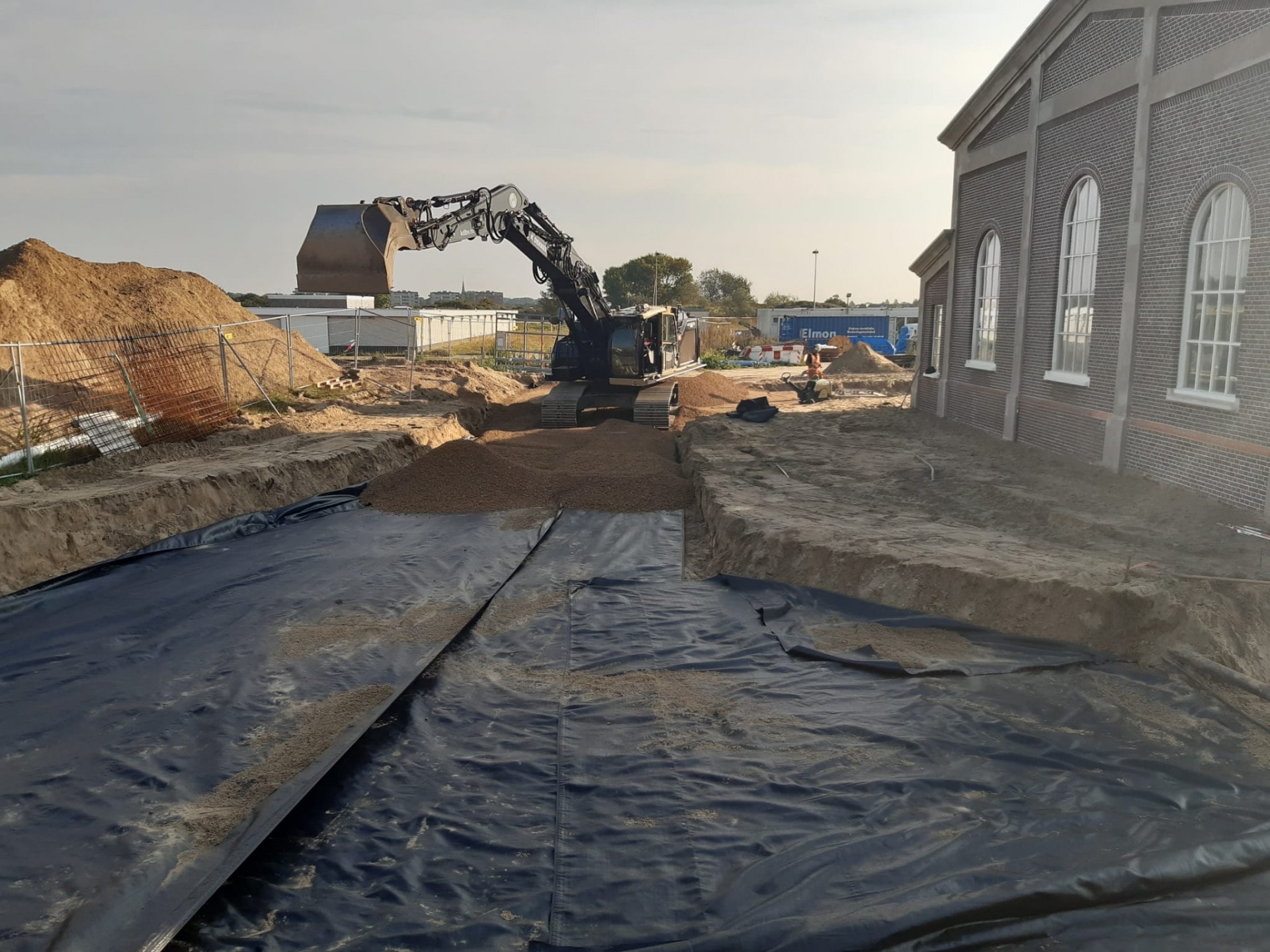
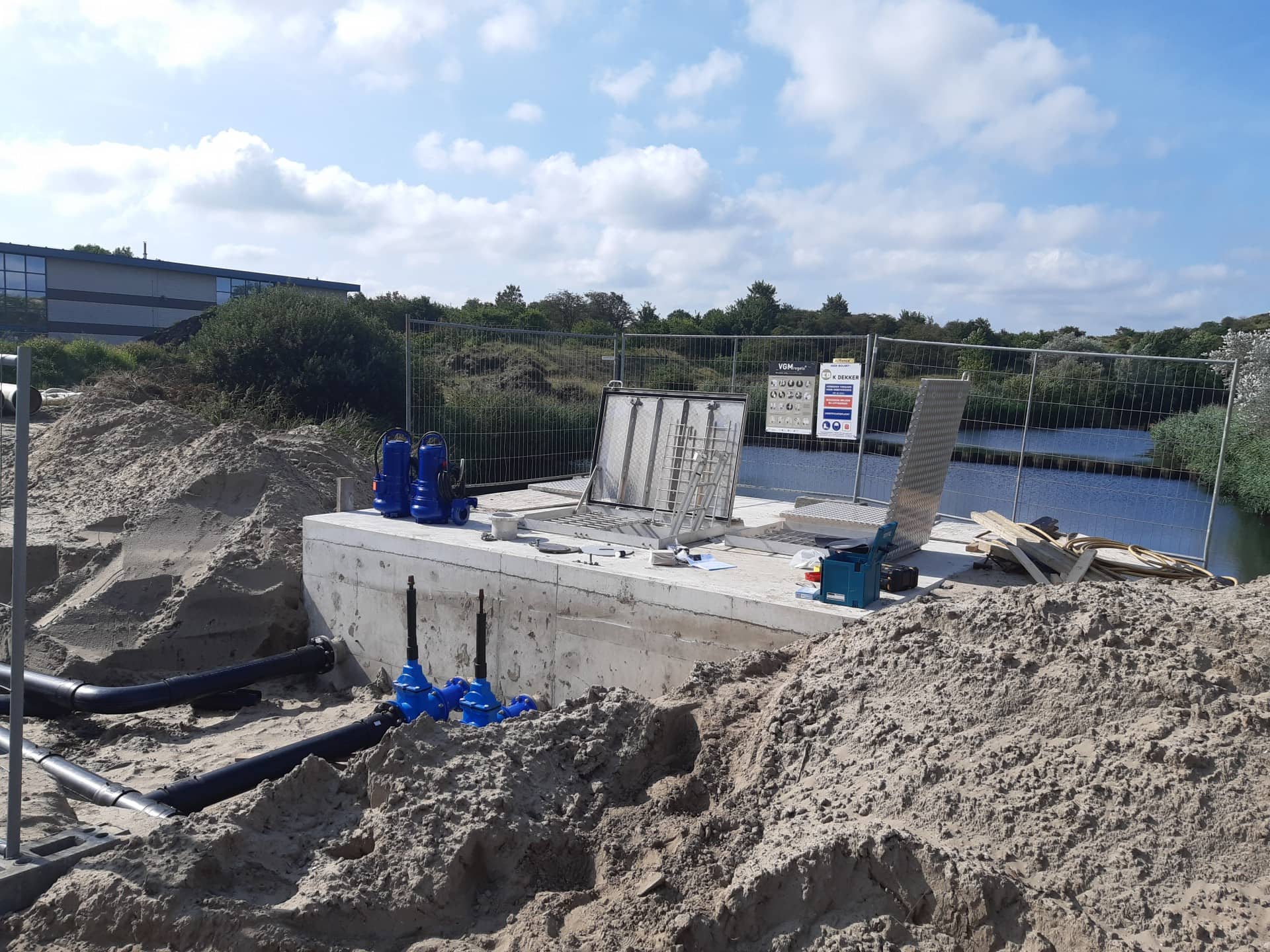
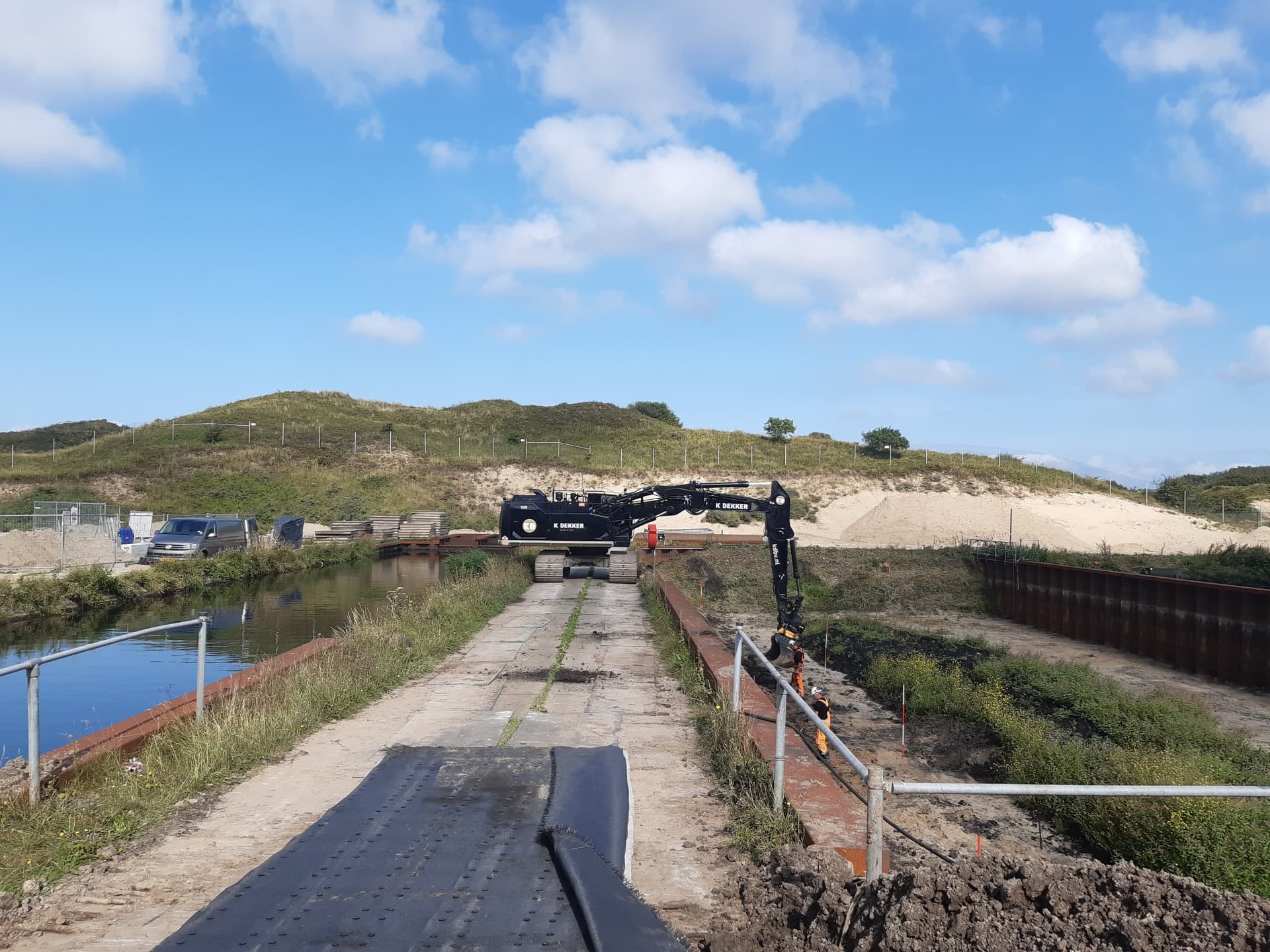